In Bestzeit zum Strukturbauteil
Präzisionswerkzeuge allgemein
Als es bei einem Sportwagenhersteller zu einem Engpass bei Strukturbauteilen kam, vertraute dieser auf das Prozess-Know-how der August Wenzler Maschinenbau GmbH. Um die mehr als sportlichen Zeitvorgaben des Autobauers erfüllen zu können, bündelten der Maschinenhersteller und der Werkzeughersteller Mapal ihr Fachwissen.
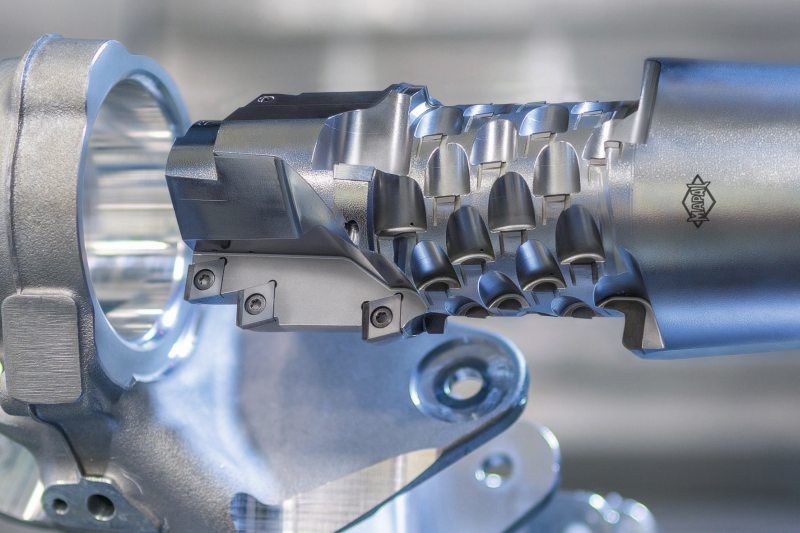
Das Kombinationsaufbohrwerkzeug mit gelöteten PKD-Schneiden und ISO-Wendeschneidplatten bietet höchstmögliche Stabilität und Standzeit in der Vorbearbeitung bei bestmöglichen Oberflächenergebnissen für definierte Oberflächen (Bild: Mapal).
Die 1954 gegründete August Wenzler Maschinenbau GmbH in Spaichingen kommt aus dem Sondermaschinenbau und hat über Jahrzehnte hinweg vor allem Rundtischmaschinen hergestellt. 2009 wurde der Betrieb von der Heller Group übernommen. Das Maschinenportfolio wurde danach komplett verändert, hin zum Standardhersteller von 5-Achs-Bearbeitungszentren. Das Unternehmen ist in der Firmengruppe für Lösungen im Bereich Strukturbauteile zuständig.
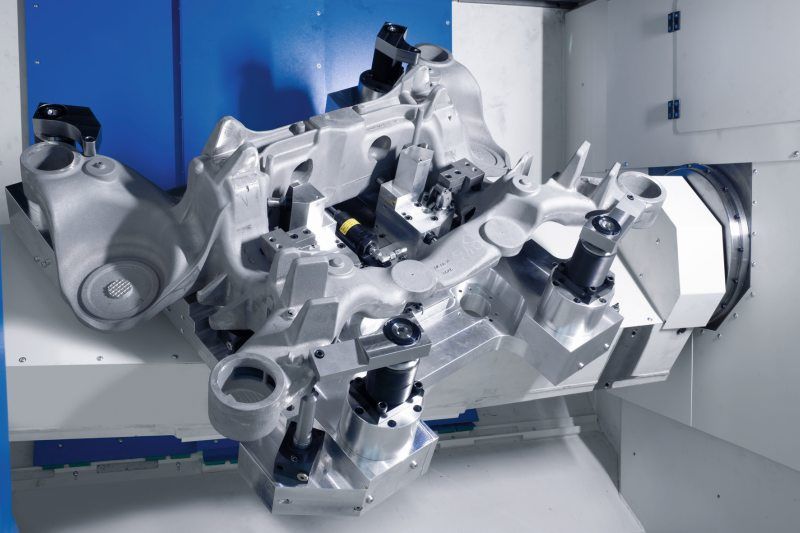
Das Strukturbauteil wird von einer speziellen Spannvorrichtung auf der Maschine »VKM« stabil gehalten und kann in einer Aufspannung von allen Seiten bearbeitet werden (Bild: Wenzler).
Das Bearbeitungszentrum »VKM« kann bis zu zwei Zentren in einem Grundbett integrieren und ermöglicht ein kompaktes Layout bei guter Zugänglichkeit. In Verbindung mit hoher Agilität und der Verwendung von Minimalmengenschmierung ist diese Maschine besonders zur Zerspanung von Aluminiumstrukturbauteilen geeignet. Ein typisches Bauteil ist der Fahrschemel, der in Fahrzeugen als Hinterachsträger fungiert. Dieser misst bis zu 1000 x 1000 Millimeter und wiegt zwischen 25 und 30 Kilogramm.
Ungewöhnliche Lösungen
Die Maschinen von Wenzler sind meist als Turnkey-Maschinen ausgelegt. »Uns ist es immer am liebsten, wenn wir neben der Maschine auch den Prozess, die Spannvorrichtung und die Werkzeuge als Komplettpaket liefern. Da haben wir die Gewissheit, dass alles gut funktioniert«, erläutert Wolfgang Wenzler, der das Familienunternehmen zusammen mit seiner Schwester Ingrid Wenzler in dritter Generation leitet.
Wenn es mal sehr schnell gehen muss, fallen Wenzler mitunter auch ungewöhnliche Lösungen ein. So wurden in der Vergangenheit auch schon Maschinen an Kunden ausgeliefert, obwohl die Konstruktion des Bauteils noch nicht abgeschlossen war und der Prozess dafür noch ausstand. Wenzler hat dafür die Entwicklung auf einer Maschine im eigenen Techcenter abgeschlossen, die in Spaichingen für solche Zwecke bereitsteht, und lieferte den Prozess nach.
Diese Maschine wurde auch genutzt, als ein Sportwagenhersteller, der nicht über eine eigene Teilefertigung verfügt, dringend 3000 Fahrschemel benötigte. Der Maschinenhersteller wurde kurzerhand zum Lohnfertiger und half dem Kunden aus der Bredouille.
Die Qualität der Bauteile und das bei Wenzler vorhandene Prozessverständnis haben den Autobauer überzeugt, und so wandte er sich vier Jahre später erneut an das Spaichinger Unternehmen. Wiederum ging es um die Fertigung von Fahrschemeln, das Unternehmen wollte eine Maschine mitsamt einem auf Minimalmengenschmierung ausgelegten Prozess kaufen. Damit startete der Sportwagenhersteller keine eigene Teilefertigung, sondern stattete seinen Zulieferer, eine Gießerei, aus, die aus eigener Kraft nicht auf die erforderliche Taktzeit für das Bauteil kam.
Von 4 Stunden auf 16 Minuten
Das Gießereiunternehmen benötigte anfangs rund vier Stunden für die mechanische Bearbeitung des Achsträgers in mehreren Aufspannungen und kam auch nach verschiedenen Optimierungen nicht unter zwei Stunden. Mit diesem Ausstoß wäre das Produktionsziel von jährlich 4000 Exemplaren der Sportwagen in Gefahr gewesen.
Anhand der Daten analysierte Wolfgang Wenzler das Bauteil und kam zu dem Ergebnis, dass eine Taktzeit von 16 Minuten möglich sei. Das konnte nach seiner Einschätzung aber nur gelingen, wenn er Mapal als Werkzeuglieferant für dieses Projekt mit ins Boot holen könnte. Die beiden Unternehmen arbeiten seit mehr als 40 Jahren zusammen und haben schon viele Projekte erfolgreich umgesetzt. Der Aalener Präzisionswerkzeughersteller bringt dabei seine Lösungskompetenz ein und es findet eine vertrauensvolle Zusammenarbeit auf Augenhöhe statt. Die besondere Herausforderung bestand dieses Mal in dem sehr hohen Zeitdruck für das Projekt, das innerhalb von zehn Wochen komplett abgeschlossen sein sollte. Eine »normale« Laufzeit für ein solches Projekt beträgt zehn Monate.
Wolfgang Wenzler würdigt die Zusammenarbeit mit Mapal: »Der gute Durchgriff in diesem Unternehmen ist imposant. Wir landen hier sehr schnell bei den richtigen Leuten bis hinauf in die Geschäftsleitung, wenn es um entsprechende Entscheidungen geht. Ohne langen Mailverkehr kommen wir auch am Telefon zu verbindlichen Zusagen, was bei diesem Projekt ganz besonders wichtig war.« Hinzu komme die Erfahrung des Werkzeugherstellers gerade im PKD-Bereich. Von dem riesigen Wissen habe auch Wenzler profitieren dürfen.
Vier entscheidende Werkzeuge
Die Analyse hat ergeben, dass die ersten vier von insgesamt 26 Werkzeugen für 60 Prozent der Taktzeit verantwortlich sind, alle weiteren werden nur relativ kurz eingesetzt. Damit wusste der Werkzeughersteller, wo er ansetzen musste, um die Performance nach oben zu bringen. Schon beim ersten Treffen konnte Mapal konkrete Vorschläge für die Werkzeugauslegung machen.
»Natürlich haben wir uns Gedanken darüber gemacht, welche Werkzeuge wir angesichts der niedrigen Stückzahlen einsetzen«, erläutert Igor Ivankovic, Component Manager Chassis & Brakes. »Da sich bei einzelnen Bearbeitungen die Schnitte doch zu langen Wegen addierten, führte kein Weg an PKD vorbei.«
Für den ersten Bearbeitungsschritt wurde mit dem Hochvorschubfräser »NeoMill-2-HiFeed« noch ein Standardwerkzeug mit Hartmetall-Wendeschneidplatten gewählt. Mit einer maximalen Schnitttiefe von 17 Millimetern fräst er die beim Gießen stehengebliebenen Steiger weg.
Als nächstes bearbeitet ein PKD-bestückter SPM-Fräser verschiedene Konturen. Um hohe Rampenwinkel beim Helixfräsen fahren zu können, ist das Werkzeug stirnseitig freigestellt. Die Vorbearbeitung der Bohrung reduziert die auftretenden Zerspankräfte und bietet bei undefinierter Aufmaßsituation mehr Flexibilität.
Für die Fertigbearbeitung der Fahrschemellager als drittem Bearbeitungsschritt arbeitete Mapal vier mögliche PKD-Lösungen aus. Da bei der Projektauslegung noch nicht bekannt war, wie die Fahrschemellager eingepresst werden, wählte man für das Aufbohrwerkzeug eine flexible Sonderlösung mit wechselbaren PKD-Schneidplatten, die sich im Radius verstellen lassen.
Das vierte Werkzeug schließlich ist ein PKD-Zirkularfräser für die Bearbeitung der Sturzstrebe, ebenfalls ein Sonderwerkzeug. Die definierte Schneidkantenbearbeitung eliminiert Vibrationen, die aus dem Bauteil oder der langen Auskraglänge des Werkzeugs entstehen können. Alle Werkzeuge sind auf den Einsatz mit Minimalmengenschmierung ausgelegt.
Zufriedenheit auf allen Seiten
Die erzielten Ergebnisse sorgten bei Wolfgang Wenzler für Erleichterung: »Mit den Werkzeugen von Mapal erzeugten wir auf Anhieb sehr gute Oberflächen, damit waren wir hochzufrieden. Das Fräsgeräusch war super satt und wir konnten sensationelle Schnittwerte fahren.« Auch mit seiner berechneten Taktzeit hatte er voll ins Schwarze getroffen: Bei der ersten Bearbeitung im Automatikbetrieb war das Bauteil ohne Optimierungen in 16 Minuten fertig.
Für die drastische Verkürzung der Taktzeit hat Sebastian Knaus, technischer Leiter bei Wenzler, mehrere Erklärungen: »Die Gießerei hatte zunächst nur eine langsamere Maschine zur Verfügung, auf der Standardwerkzeuge benutzt wurden, die viele Wege benötigten. Unser Performance-Ansatz war dem von vornherein überlegen. Hinzu kam, dass zuvor mit drei Aufspannungen gearbeitet wurde.«
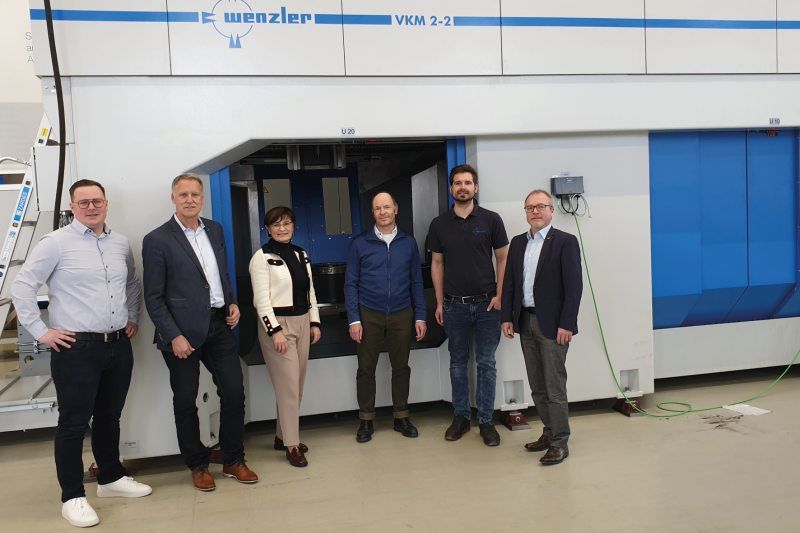
Haben für das anspruchsvolle Projekt ihr Know-how gebündelt (v. l.): Igor Ivankovic und Peter Krafft (Mapal), Ingrid und Wolfgang Wenzler sowie Sebastian Knaus (Wenzler) und Sven Frank (Mapal). Im Hintergrund eine Maschine des Typs »VKM 2-2« mit jeweils zwei Spindeln und zwei autarken Kammern (Bild: Mapal).
Weil die Brücke der »VKM«-Maschine relativ schlank baut, konnten Bearbeitungen auch »über Kopf« ausgeführt werden, was die Fertigung des gesamten Bauteils in einer einzigen Aufspannung ermöglichte. Das Projekt in Spaichingen hat gezeigt, dass mit der eingesparten Laufzeit und den entsprechend reduzierten Maschinenstunden mit teureren Lösungen sogar bei relativ geringen Stückzahlen niedrige Costs per part möglich werden.