Bis zu 90 % schneller schlichten
Präzisionswerkzeuge allgemein
Das junge Familienunternehmen PitMaTec Zerspanung GmbH profiliert sich als Fertiger bei komplexen Zerspanungsprojekten ab Losgröße 1 bis hin zur Serienfertigung. Ohne die enge Zusammenarbeit mit Technologiepartnern wie dem Zerspanungsexperten Walter wären dabei Projekte wie die Bearbeitung eines Freiformgehäuses wirtschaftlich kaum darstellbar.
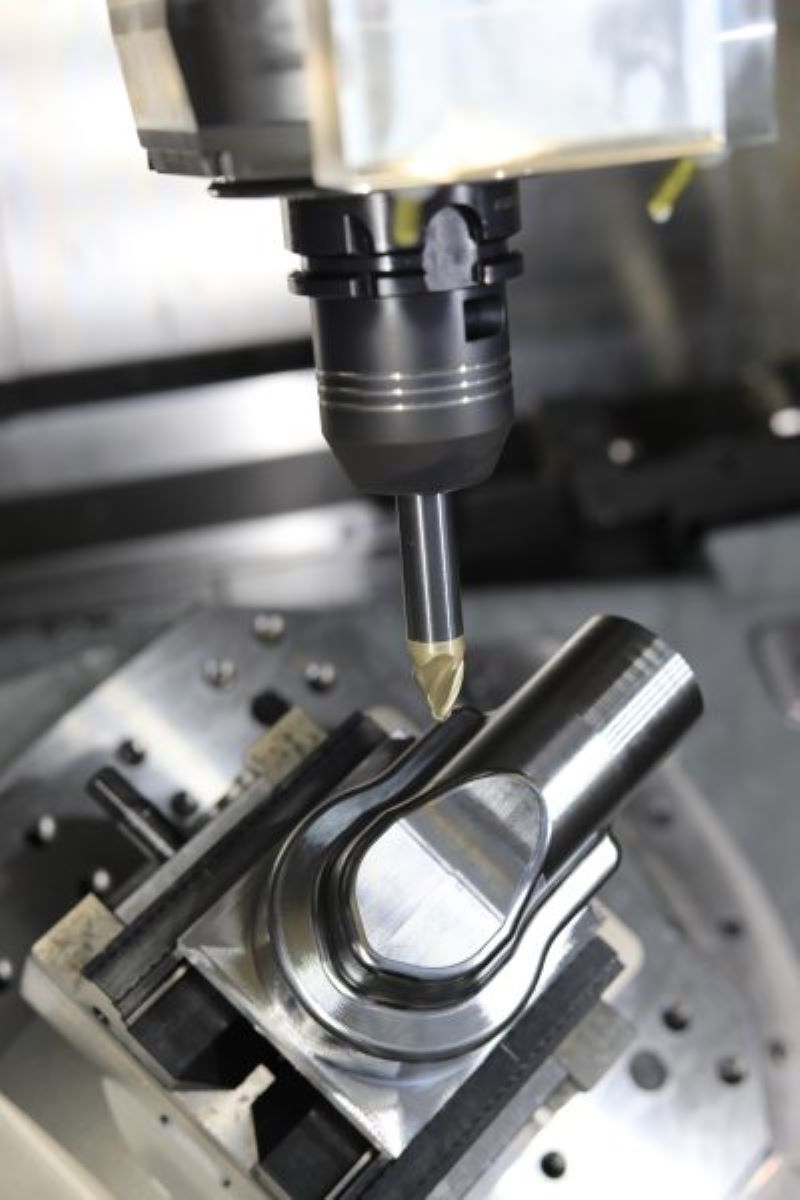
Wirtschaftliche Bearbeitung: Die Kreissegmentgeometrie sowie die Beschichtung ermöglichen das Fräsen mit dynamischen Kontaktpunkten und damit einen deutlich höheren Zahnvorschub (Bild: Walter).
Detlef Pitan, Gründer und Geschäftsführer von PitMaTec, sagt: »Wir haben uns sehr intensiv darüber Gedanken gemacht, wie wir uns als Neueinsteiger am Markt positionieren wollen. Uns war schnell klar, dass wir nicht – wie viele Neugründungen in der Zerspanungsindustrie – als Garagenfirma starten möchten.
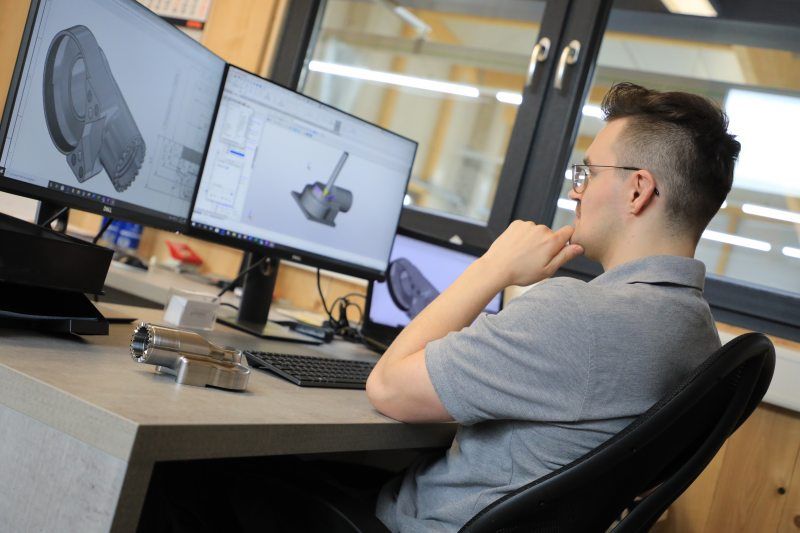
PitMaTec hat sich dafür entschieden, die Prozesse von Beginn an als Industrie 4.0 aufzusetzen, digital basiert und komplett vernetzt (Bild: Walter).
Wir haben uns dafür entschieden, unsere Prozesse von Beginn an als Industrie 4.0 aufzusetzen, digital basiert und vor allem komplett vernetzt. Als Lohnfertiger können wir so extrem schnell neue Zerspanungsprozesse planen und aufsetzen, gerade bei komplexen Bauteilen oder Bearbeitungsschritten. Der Vorteil: Kurze Wege, neueste Technologien und ein Team aus Digital Natives, das auch die Programmierung komplett selbst leistet.«
Entsprechend intensiv hat der Betrieb in die technische Ausstattung investiert: In der Halle stehen eine DMG Mori »CTX beta 1250 TC« und eine Hermle »C 42 U dynamic«. Auf einer Portalmessmaschine von Zeiss können die fertigen Bauteile oder auch Zwischenschritte direkt selbst geprüft werden.
Zusammenarbeit auf Augenhöhe
Für die Auswahl von Technologiepartnern haben Detlef Pitan und sein Sohn David klare Kriterien definiert. Denn ohne agile und zuverlässige Partner in einem strategisch so zentralen Bereich wie den Zerspanungswerkzeugen lässt sich der Anspruch des Unternehmens kaum umsetzen. Detlef Pitan erklärt: »Am Wichtigsten ist für uns die schnelle Erreichbarkeit und Partnerschaft auf Augenhöhe. Wir wollen nicht, weil wir klein sind, der Letzte in der Nahrungskette sein.
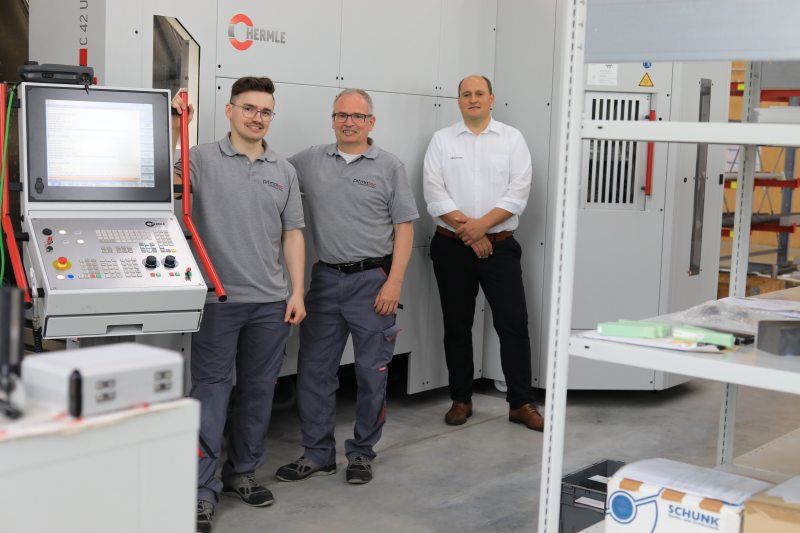
V. l. n. r.: David und Detlef Pitan (PitMaTec) sowie Josef Spaag (Walter), der von Beginn an in die Planung und Umsetzung des Zerspanungsprozesses eingebunden war (Bild: Walter).
Wir sind technologisch ziemlich weit vorn, dafür brauchen wir einen Partner, der uns Zugang zu seinen aktuellsten Technologien und Innovationen gibt. Schnell von fachlich kompetenten und erfahrenen Vertriebsmitarbeitern betreut zu werden, ist für uns wesentlich. Bei Walter hatten wir nach einigen Gesprächen das sichere Gefühl, dass man dort versteht, wohin wir wollen − eine Einschätzung, die sich in der Zusammenarbeit bewahrheitet hat.«
Das Ellwanger Start-up wird von Walter durch Josef Spaag betreut. Der technische Berater umreißt den Umfang der Zusammenarbeit: »Von Beginn an in die Planung und Umsetzung von Zerspanungsprozessen eingebunden zu sein ist für den Kunden und uns eine ideale Situation. PitMaTec hat keine Scheu vor Innovationen oder ungewöhnlichen Herangehensweisen an eine Herausforderung. Beim Einsatz neuer Werkzeuge lernen wir quasi gemeinsam, wie auch beim aktuellen Projekt mit dem neuen Kreissegmentfräser.
Bevor wir an konkreten Projekten gearbeitet haben, ging es erst einmal darum, den Betrieb mit einem Sortiment an Zerspanungswerkzeugen und Aufnahmen auszustatten, um einen möglichst universellen Einsatz zu ermöglichen. Zusätzlich wurde ein Werkzeugausgabesystem mit der entsprechenden Verwaltungssoftware installiert, die eine möglichst lückenlose Werkzeugversorgung ermöglicht. In der modernen Zerspanung geht es um mehr als drehen, fräsen, bohren und gewinden. Es geht darum, Ziele schneller, sicherer und präziser zu erreichen – mit Lösungen, die Projekte effektiver und effizienter machen.«
Anspruchsvolle Bearbeitung wirtschaftlich umsetzen
Für die Durchführung des anspruchsvollen Projekts »Future-Finishing-Wiko-Gehäuse« war die enge Zusammenarbeit beider Unternehmen wesentlich. David Pitan, Meister Zerspanungstechnik und Fertigungsleiter, erklärt: »PitMaTec kommt auch dann ins Spiel, wenn der bisherige Zulieferer eines Herstellers erhöhte Qualitätsanforderungen oder engere Zeitfenster nicht abbilden kann oder ein Werkstück eine komplexere Geometrie erhält. Das Wiko-Gehäuse ist so ein Fall. Wir haben Walter schon ganz früh in den Planungsprozess einbezogen. Gemeinsam haben wir einen Prozess entwickelt, der das gewünschte Ergebnis zu wirtschaftlich sinnvollen Parametern bringt.«
Die Herausforderung, die das Bauteil an die Zerspanung stellt, erschließt sich nicht auf den ersten Blick: Die Grundgeometrie ist gut darstellbar, die Schwierigkeiten liegen dagegen ganz wörtlich an der Oberfläche. Sie ist 3D-freiflächengeformt, außerdem ist eine hohe Oberflächenqualität gefordert. Schon das ist technisch anspruchsvoll und aufwendig, und durch den Werkstoffwechsel erhöhte sich die Komplexität des Projekts weiter. In einer anderen Version wird das Gehäuse aus EN AW-7075 gefertigt, beim aktuellen Projekt hingegen aus 16MnCr5. Um für die Freiflächenform die entsprechende Oberflächenqualität zu erreichen, müsste mit einem konventionellen Radiuskopierfräser mit Zeilensprüngen von 0,1 Millimetern zerspant werden. So lässt sich das jedoch wirtschaftlich nicht darstellen, sondern nur mit den neuesten technischen Mitteln – und einer Zerspanungsstrategie, die diese bestmöglich einsetzt.
Hohe Prozesssicherheit bei verkürzter Bearbeitungszeit
Die Wiko-Gehäuse werden auf dem fünfachsigen Hermle-Bearbeitungszentrum gefertigt. Das Bearbeitungszentrum bringt nicht nur die notwendige Beweglichkeit im Raum, sondern auch die nötige Dynamik mit, um das Werkstück mit wenigen Umspannungen fertigen zu können. Wirklich ausnutzen lassen sich die Möglichkeiten der Maschine in 5-Achs-Simultanbearbeitung nur mit dem entsprechenden Zerspanungswerkzeug. Den entscheidenden Faktor für den Erfolg des Projekts sieht David Pitan deswegen in der Chance, bei Walter auf Zerspanungstechnologien zugreifen zu können, die sich noch im Feldteststadium befinden. Angedacht war ursprünglich der Einsatz eines Radiuskopierfräsers, Josef Spaag brachte als Lösung einen neuen Kreissegmentfräser »MD838 Supreme« in der konischen Variante ins Spiel. Der hatte bereits im Walter Technology Center und in Feldtests gezeigt, dass sich Oberflächen bis zu 90 Prozent schneller als im bisher angewendeten Verfahren schlichten lassen.
Die Kreissegmentgeometrie sowie die Beschichtung ermöglichen das Fräsen mit dynamischen Kontaktpunkten und damit einen deutlich höheren Vorschub. Er beträgt pro Zahn 0,17 Millimeter, die Schnittgeschwindigkeit beträgt 600 Meter pro Minute. Gefräst wird in Zeilensprüngen von zwei und drei Millimetern. Insgesamt liegt die Vorschubgeschwindigkeit bei gut 8000 Millimetern pro Minute. Der neue Fräser ist nicht nur besonders schnell: Beschichtung und Geometrie ermöglichen eine sehr hohe Konformität zu den Spezifikationen des Bauteils bereits beim Schlichten, was den Aufwand fürs Polieren reduziert.
Für PitMaTec sind Prozesssicherheit und Wirtschaftlichkeit die ausschlaggebenden Faktoren: Mit der »Future-Finishing-Strategie« erreicht das Unternehmen eine Bearbeitungszeit pro Werkstück, die den Auftrag überhaupt erst wirtschaftlich macht.