Werkzeuge für Hightech-Werkstoffe
Drehwerkzeuge, galvan. Diamantwerkzeuge PKD-CBN
Diesen und viele weitere Fachbeiträge lesen Sie in der aktuellen Ausgabe des Jahresmagazins »Maschinenbau + Metallbearbeitung«, das Sie über diesen Link bestellen können.
Die Herrmann CNC-Drehtechnik GmbH aus Hohenlinden bei München hat sich einen sehr guten Ruf als Zulieferer in der Luftfahrtindustrie erarbeitet. Für die Bearbeitung von Hightech-Werkstoffen liefert der Hersteller von Präzisionswerkzeugen Horn aus Tübingen die Werkzeuge, die den hohen Belastungen standhalten und die Qualitätserwartungen erfüllen.
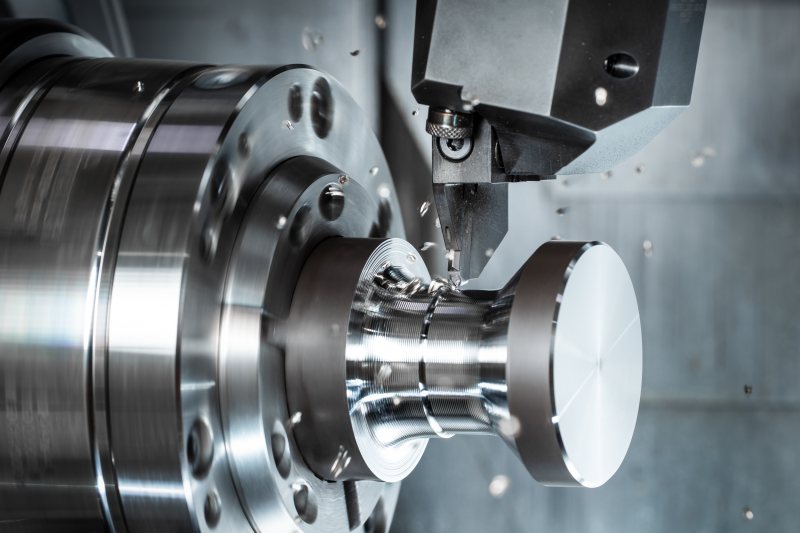
Das trochoidale Drehen eignet sich für die Fertigung tiefer und breiter Einstiche, bei denen ein hohes Spanvolumen generiert werden muss (Bild: Horn/Sauermann).
In Flugzeugen wird die Bewegung der Flügelvorderkanten (Slats) und der Flügelenden (Flaps) über eine Mechanik im Flügelinneren gesteuert. Hier kommt zum Beispiel ein Stehlager der Herrmann CNC-Drehtechnik zum Einsatz. Das Lager überträgt das Drehmoment des Gestänges und gleicht das axiale Spiel über eine Verzahnung aus. Darüber hinaus dient das Stehlager als winkelbewegliche Kupplung zwischen den Wellen. »Horn entwickelt ständig gute Verbesserungen bei den Werkzeugbeschichtungen und den Schneidgeometrien. Als Zulieferer in der Luftfahrtindustrie arbeiten wir täglich mit besonderen Werkstoffen, welche nicht immer leicht zu zerspanen sind«, erklärt Produktionsleiter Stefan Schubel. Für die Stechbearbeitungen der Nabe und der Welle des Stehlagers setzt Schubel mit seinem Team daher auf die Werkzeuge der Paul Horn GmbH aus Tübingen.
Die Lagernabe wird aus 1.4548 (X5CrNiCuNb17-4-4) gefertigt, einem Stahl mit hoher Festigkeit und Zähigkeit, der dank hoher Korrosionsbeständigkeit und dank sehr guten mechanischen Eigenschaften häufig in der Luft- und Raumfahrt zum Einsatz kommt. Der große und tiefe Einstich wird mit dem trochoidalen Stechverfahren in das Werkstück gefertigt. Zum Einsatz beim Schruppen kommt hierbei eine Vollradius-Stechplatte aus dem System »S229« mit einem Radius von 2 mm. Als Substrat schlug der Werkzeughersteller die Sorte »AS66« vor. Diese Kombination ist sehr gut für die Zerspanung solcher Werkstoffe geeignet.
Trochoidales Drehen
Das trochoidale Drehen eignet sich besonders für die Fertigung tiefer und breiter Einstiche, bei denen ein hohes Spanvolumen generiert werden muss. »Wir wenden das Verfahren seit rund zwei Jahren an. Als CAM-System nutzen wir ›Esprit‹. Die Software war eine der ersten, welche die Möglichkeit zum trochoidalen Stechen geboten hat«, sagt Schubel. Der Stechprozess gestaltet sich wie folgt: Der 30 mm breite und 15 mm tiefe Einstich wird mit der Vollradius-Wendeschneidplatte mit einer Schnittgeschwindigkeit von vc = 140 m/min bei einer Schnitttiefe von ap = 1 mm trochoidal geschruppt. Der Vorschub ist mit fn = 0,25 mm-1 programmiert. Das Schlichtaufmaß liegt bei 0,2 mm. Beim Schlichten kommt ebenfalls eine Schneidplatte des Systems »S229« zum Einsatz. Die Schlichtbearbeitung geschieht von zwei Seiten mit einer 3 mm breiten Stechplatte. Der Eckenradius beträgt 0,2 mm. Die Gesamtfertigungszeit des Einstiches liegt bei unter zwei Minuten. »Durch das Stechverfahren haben wir bei dem schwer zu zerspanenden Werkstoff keine Probleme mit langen Spänen«, so Schubel.
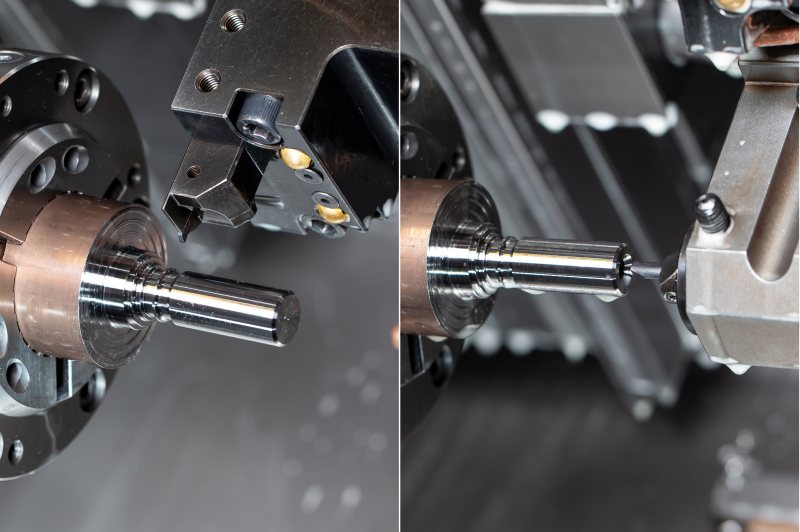
Fertigung der Einstiche mit dem Stechsystem »223« (li.) und Ausdrehen der Bohrung mit dem System »Supermini Typ 105« (re.) (Bild: Horn/Sauermann).
Die Welle des Stehlagers besteht aus dem Werkstoff SAE 51431 (1.4044), vergütet auf 1350 bis 1500 N/mm². »Der Bezug dieses Stahles in Sonderqualität gestaltet sich häufig schwierig. Wir beziehen das Material direkt beim Hersteller in Frankreich und bestellen es deshalb nicht in vielen Durchmesservarianten. Die geringeren Stückzahlen der zu fertigenden Bauteile rechtfertigen auch die teilweise hohen Abtragswerte. Sonst würden wir nicht aus einem 55 mm Rundmaterial eine 26,4 mm Welle drehen«, erzählt der Produktionsleiter. Die 5 mm breiten Einstiche übernimmt eine Schneidplatte des Systems »223«. Die Standzeit pro Schneide liegt hier bei über 300 Werkstücken. Das Innenausdrehen der Bohrung und die 45-Grad-Fase fertigt eine Schneidplatte des Typs »Supermini 105«. Das Schlichten des Axialeinstichs übernimmt ebenfalls ein »Supermini«. »Die geforderten hohen Oberflächengüten konnten wir mit den Werkzeugen problemlos einhalten«, so Schubel.
Qualität im Fokus
Im Mittelpunkt steht bei der Fertigung immer die Qualität der Bauteile. Für die strenge Luftfahrtzertifizierung nach DIN EN 9100 sind ein sauberer Arbeitsplatz, hochqualifiziertes Personal und eine Qualitätssicherung mit Hightech-Messmaschinen bedingungslose Voraussetzungen. Es sind nicht nur die offiziellen Zertifizierungen, auch die Kunden von Herrmann besuchen den Betrieb für regelmäßige Audits. »Sauberkeit, präzises Arbeiten und die ständige Qualitätskontrolle sind für unsere tägliche Arbeit ein absolutes Muss«, erzählt Schubel. So fertigt der Betrieb alle Bauteilklassen für die Luftfahrtindustrie, welche von Klasse 3 bis Klasse 1 reichen. Ein Klasse-1-Bauteil ist das kritischste Bauteil, bei dessen Versagen wird die Sicherheit des Fluggeräts massiv beeinträchtigt. Beim Versagen eines Bauteils der Klasse 2 entsteht eine schwere Beeinträchtigung des Fluggeräts, aber die Landung ist noch möglich. Der Ausfall eines Klasse-3-Bauteils wirkt sich nicht auf die Funktionsweise aus.
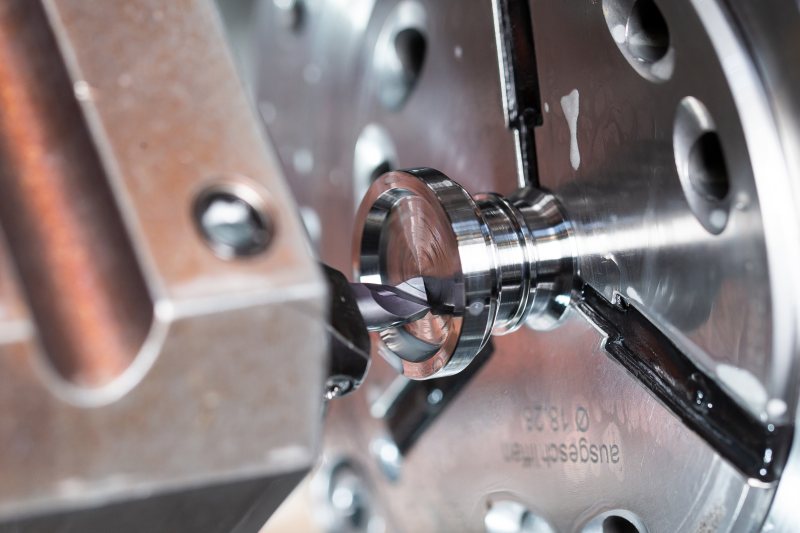
Plandrehen des Axialeinstiches mit dem »Supermini 105« (Bild: Horn/Sauermann).
Lösungen für die Luftfahrt
Gegründet im Jahr 1986 in einer größeren Garage, vereint die Herrmann CNC-Drehtechnik GmbH heute auf einer Fläche von 7000 Quadratmetern ihre Produktion und Verwaltung in Hohenlinden bei München. Mit 100 Mitarbeitern haben sich die Bayern auf die Herstellung von Bauteilen der Luft- und Raumfahrttechnik spezialisiert. Durch das Knowhow bei der Zerspanung von sensiblen Bauteilen und schwer zerspanbaren Werkstoffen hat sich das Unternehmen bei vielen großen Luft- und Raumfahrtkonzernen einen sehr guten Ruf und den Status »preferred supplier« erarbeitet. Seit über 25 Jahren arbeiten Herrmann und Horn schon zusammen an gemeinsamen Aufgaben. »Es ist immer ein sehr angenehmes und zielführendes Miteinander mit den technischen Beratern und den Mitarbeitern im Innendienst. Wir freuen uns auch auf die zukünftigen Aufgaben, bei denen wir die Werkzeuge einsetzen, und hoffen, dass Horn die Zuverlässigkeit und die hohe Lieferperformance auch in der Zukunft beibehält«, schließt Schubel.
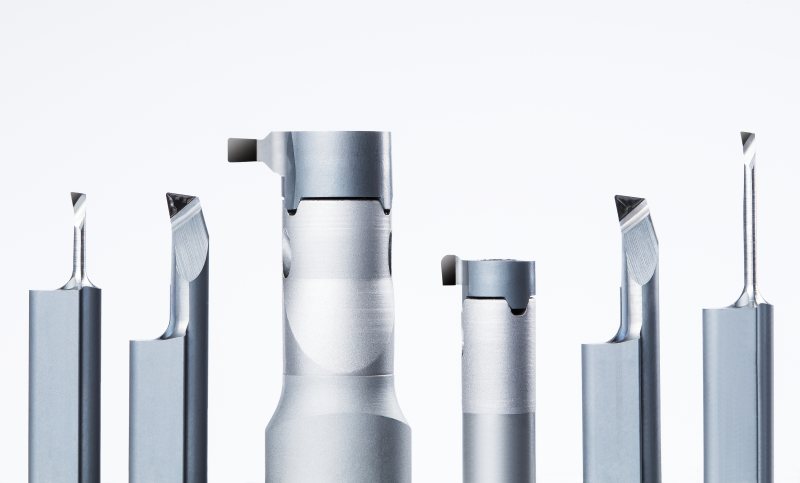
Diamantwerkzeuge aus polykristallinem Diamant (PKD) zur Bearbeitung hochfester Werkstoffe (Bild: Horn/Sauermann).
Für Hersteller in der Luft- und Raumfahrt bietet Horn als Technologiepartner passende Lösungen für die Zerspanung von Hightech- und konventionellen Werkstoffen. Durchdachte Zerspanungsstrategien sind unverzichtbar für mehr Wirtschaftlichkeit und zur Steigerung der Wettbewerbsfähigkeit, gerade bei hochfesten Werkstoffen wie Titan-, GFK-/CFK-Verbundwerkstoffen und Hochtemperaturmaterialien.
Die Werkzeugkonzepte des Tübinger Herstellers steigern die Effizienz und können bei hoher Prozesssicherheit und Qualität die Bearbeitungszeiten deutlich reduzieren. Beispiele sind Diamantwerkzeuge aus polykristallinem Diamant (PKD). Mit ihren harten, verschleißfesten und scharfen Schneiden erreichen sie hohe Standzeiten bei nichteisenhaltigen Werkstoffen. Beim Bearbeiten von CFK- und GFK-Verbundstoffen bieten CVD-Dickschicht-Diamantwerkzeuge mit präzisionsgelaserter Schneidkante ein hohes Potenzial zur Steigerung der Effizienz. Die Schneiden bestehen bis zu 99,9 Prozent aus reinem Diamant, bieten die höchstmögliche Wärmeleitfähigkeit und erreichen eine bis zu zehnfach höhere Kantenschärfe als bisherige PKD-Schneiden.
Link zum Produkt: Hartmetallwerkzeugfabrik Paul Horn – Übersicht Drehwerkzeuge.