Hochgenaue Fertigungsüberwachung mit Dickenmessung
Mess- und Prüfgeräte, Mess- und Prüfmaschinen
Brammen, Bleche oder Bänder aus Stahl, Aluminium oder Buntmetallen werden mit immer geringeren Fertigungstoleranzen hergestellt. Eine entscheidende Messgröße im Produktionsprozess ist die Metall-Dicke. Für die hochgenaue Dickenmessung eignen sich Laserscanner von Micro-Epsilon. Die Vorteile liegen im Vergleich zu herkömmlichen Prüfmethoden vor allem in gesteigerter Effizienz durch erhöhte Präzision und reduzierte Kosten.
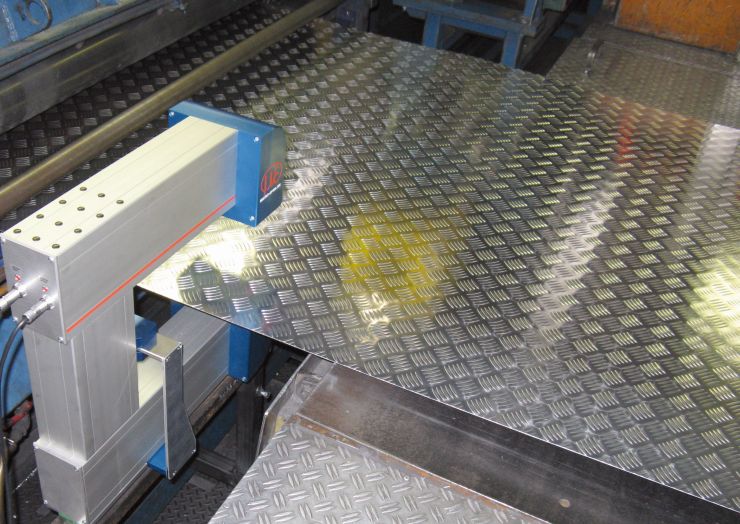
Micro-Epsilon bietet sehr präzise Messanlagen für die Blechdickenmessung. Ihre Stärken zeigen Laser-Profil-Sensoren insbesondere bei der Erfassung von strukturierten Oberflächen. Bilder: Micro-Epsilon
Stahl, Aluminium und Buntmetalle sind wichtige Basismaterialien der industriellen Produktion. Bei ihrer Bearbeitung spielt unter anderem die Einhaltung von Maßtoleranzen eine wichtige Rolle. Werden beispielsweise Bauteile an verschiedenen Orten gefertigt und anschließend zusammengefügt, so gilt es die in der Ausschreibung vorgeschriebenen und meist sehr geringen Toleranzen einzuhalten. Nur wenn alle Zulieferer ihre Bauteile mit den vorgegebenen Maßen produzieren, ist ein späteres Zusammenfügen ohne aufwendige Nacharbeit möglich. Zudem werden bei korrekten Abmessungen Material, Zeit und damit Kosten eingespart. Denn sowohl die Nacharbeit als auch ein höherer Materialverbrauch, der gleichzeitig auch einen höheren Ressourcenverbrauch bedeutet, verursachen in erster Linie Mehrkosten. Diese Mehrkosten lassen sich durch den Einsatz moderner Messsysteme vermeiden.
Micro-Epsilon bietet mit den C- und O-Rahmensystemen präzise und wirtschaftliche Lösungen für die Fertigungsüberwachung. Mit ihnen ist eine einfache, geometrische Fertigungsüberwachung mittels integrierter Laserscanner möglich. Sie werden zum Überwachen und Regeln im Warm- und Kaltwalzbereich eingesetzt. Sehr wichtige Messgrößen sind die Dicke und die Breite des Materials, da sich diese wesentlich auf nachfolgende Prozesse auswirken.
Die eingesetzten Laserscanner messen dabei berührungslos und verschleißfrei. Die umfangreiche Analyse-Software bietet zahlreiche Diagramme für Quer- und Längsprofile, die SPC-Analyse und die Fehlfarbendarstellung.
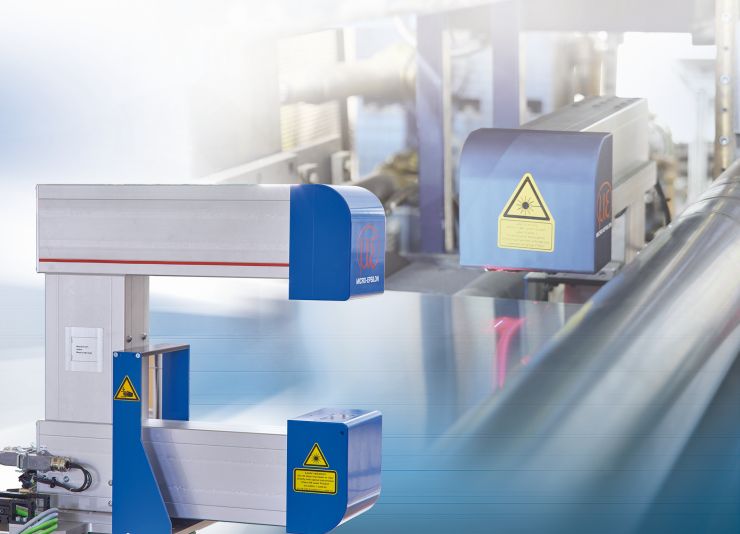
C-Rahmen eignen sich vor allem bei Anwendungen an schmalen Bändern, da bei wachsender Materialbreite die Schwingungsanfälligkeit des oberen Gurtes zunimmt. Bild: Micro-Epsilon
Besser messen
Die Messung mit optischen Verfahren auf Basis der Laserlinien-Triangulation hat sich bewährt. Auch bei rauen Umgebungsbedingungen erfolgen stabile, verschleißfreie und dynamische Messungen über das gesamte Band hinweg. Berührende Verfahren dagegen, die von oben und unten auf das Bandmaterial erfolgen, sind dadurch auch mit einem gewissen Verschleiß verbunden. Zudem wird lediglich an einzelnen Punkten, nicht aber über das ganze Band hinweg gemessen. Die Messergebnisse sind somit ungenau und wenig zuverlässig. Auch radiometrische Verfahren auf Basis isotoper Strahlung oder einer Röntgenquelle sind oft problematisch, da die Zuverlässigkeit von der Legierung und der Materialbeschaffenheit abhängt. Zudem bedingt dieses Verfahren regelmäßige Sicherheitsprüfungen und hohen Aufwand für Strahlenschutz. Des Weiteren müssen Materialkennwerte auf das Messsystem angepasst werden, was häufig mit aufwendigen Kalibrierungen einhergeht.
Messungen mittels der oben genannten Laserlinien-Triangulation, auf der Micro-Epsilon-Systeme basieren, sind besser geeignet. Die Sensoren wirken nicht auf das Material ein, wodurch kein Verschleiß entsteht. Auch bei industriellen Umgebungsbedingungen wie Dampf oder dem Einsatz von Schmierstoffen lassen sich mit entsprechenden Maßnahmen zuverlässige und genaue Messungen generieren. Laserlinien-Triangulatoren arbeiten außerdem materialunabhängig und können auch bei Spiegelungen in Verbindung mit glänzenden Oberflächen eingesetzt werden. Die hochdynamischen Messungen, die mit 128.000 Messpunkten pro Sekunde erfolgen, liefern hohe Präzision, auch für strukturiertes Material wie Warzen-, Tropfen- und Riffelblech. Selbst wenn durch die vorherrschenden Umgebungsbedingungen nur die Hälfte der Messwerte nutzbar wäre, ließe die hohe Datenrate der Sensoren noch immer stabile Messungen zu. Dies ist im Vergleich zu Punkt-Sensoren ein deutlicher Vorteil. Dieser Effekt tritt besonders bei der Bearbeitung von Bändern oder Blechen in Fräslinien auf, wenn Messungen auf hochspiegelnden Oberflächen durchgeführt werden müssen. Die Vorteile von Laserlinien-Sensoren werden hier besonders offensichtlich. Die Mächtigkeit der von den Sensoren gelieferten Punktewolke ermöglicht bei dieser Applikation eine sehr performante Signalverarbeitung. Mit entsprechenden Filteralgorithmen können ungültige oder nicht plausible Werte entfernt und ein präziser Messwert erzeugt werden.
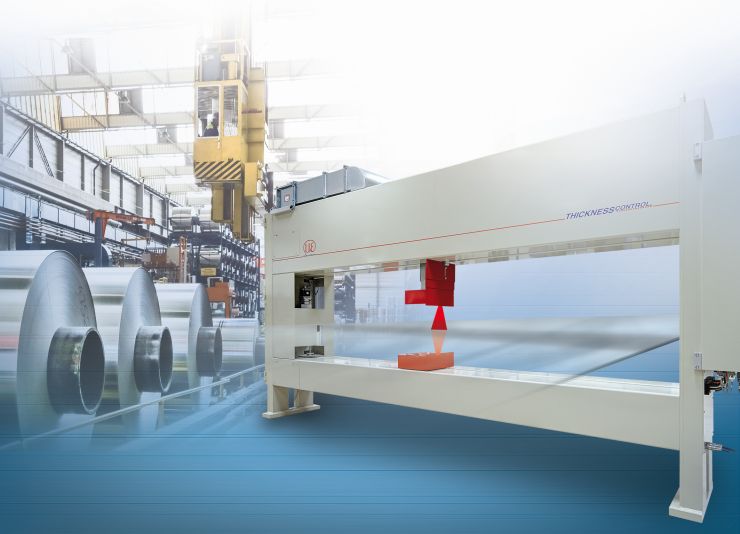
Die Messung mit optischen Verfahren auf Basis der Laserlinien-Triangulation hat sich bewährt. Bild: Micro-Epsilon
Verarbeitung von Coils
Bei der Verarbeitung von Coils können beispielsweise große vertikale Bewegungen entstehen. Die höhere Informationsdichte, die von einem Profilsensor generiert wird, zeigt hier ihre Vorteile. Beim Profilsensor wird der Laserpunkt zu einer Linie aufgeweitet. Der Messwert ergibt sich aus einer Best-Fit-Geraden durch die vom Sensor erzeugte Punktewolke. Damit ist die Relation Abstand zu Auflösung des Liniensensors erheblich besser als die des Punktsensors, da die Änderung dieser Gerade aus dem Zusammenspiel vieler Teilauflösungen berechnet wird. Es stehen wesentlich mehr Messwerte auf einer größeren Fläche zur Verfügung, die gemittelt eine höhere Präzision schaffen. Durch die Best-Fit-Gerade wird dieses Merkmal in Summe so erhöht, dass letztlich die Auflösung des Liniensensors bei einem größeren Messabstand besser ist als die des Punktsensors. Mithilfe der oben angeführten Maßnahmen wird mit Linien-Scannern ein Arbeitsspalt von 190 Millimetern mit einem Messbereich von 40 Millimetern und einer Präzision von ±5 Mikrometern erreicht, während mit Punktsensoren in diesen Bereichen nur ungefähr ±25 µm realisiert werden können.
Bei der differentiellen Dickenmessung mit Abstandssensoren ist der konstante Sensorabstand von Bedeutung. In der Regel werden zwei unterschiedliche Konstruktionstypen eingesetzt, die aufgrund ihrer Form als sogenannte C-Rahmen oder O-Rahmen bezeichnet werden. Beim C-Rahmen werden die Sensoren an Ober- und Untergurt fest montiert und der Rahmen wird als Einheit bewegt, um die Messposition zu erreichen. C-Rahmen eignen sich vor allem bei Anwendungen an schmalen Bändern, da bei wachsender Materialbreite die Schwingungsanfälligkeit des oberen Gurtes zunimmt. Zur Kalibrierung des C-Bügels fährt während des Coil-Wechsels automatisch ein Masterteil in den Messspalt und gleicht damit das System für neue Messungen ab. Der Vorteil des C-Rahmens liegt darin, dass er beim Einfädeln oder in Gefahrensituationen durch sogenannte Skieffekte (Band krümmt sich einseitig nach oben) oder Alligator-Effekte (Band krümmt sich nach oben und unten) am Bandanfang komplett aus der Linie entfernt werden kann. Dazu benötigt er allerdings seitlich zum Band Platz, der vor allem im Bereich der Servicecenter oft nicht vorhanden ist.
Hier eignet sich der O-Rahmen mit seiner kompakten Bauform. Gerade aufgrund des konstanten Messspalts, der ein entscheidendes Kriterium für die Präzision einer solchen Anlage darstellt, bietet der O-Rahmen große Vorteile. Diese Anlagenbauform basiert auf einem stabilen Rahmen, der in die Produktionslinie integriert wird. Mittels des steifen Rahmens können Bandbreiten von bis zu 4000 Millimeter auf Dicke, Profil, Breite et cetera getestet werden. Auch diese Anlage verfügt über eine Autokalibriereinheit. Die Sensorik traversiert während der Messung ständig über das Metallband und erfasst damit Profildaten über die gesamte Materialbreite.
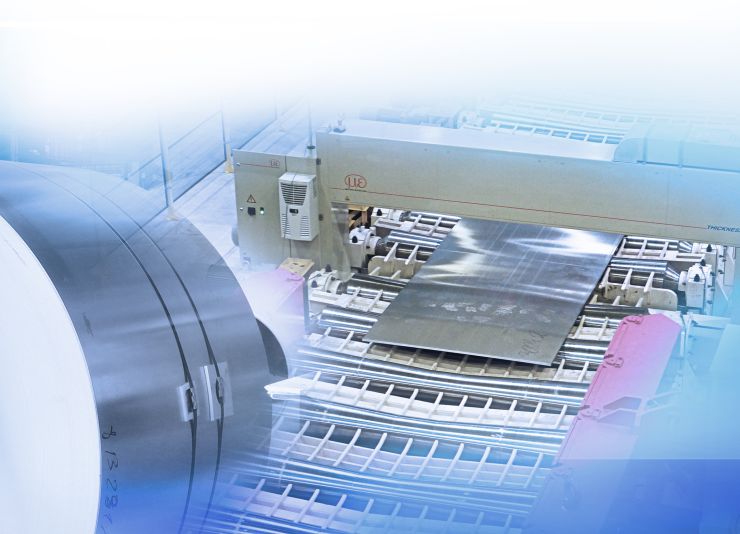
Auch bei rauen Umgebungsbedingungen erfolgen stabile, verschleißfreie und dynamische Messungen über das gesamte Band hinweg. Bild: Micro-Epsilon
Messung von Laminatblechen
Eine weitere Applikation, für die die Laserlinien-Sensoren prädestiniert sind, ist die Dickenmessung von Laminatblechen. Durchstrahlende Verfahren können hier nicht verwendet werden. Sind die Laminatbleche beispielsweise aus Außenblechen und einer Stegstruktur im Inneren gefertigt, so messen durchstrahlende Verfahren nur den Materialanteil im Messspalt, aber nicht die Maßhaltigkeit des Produkts. Die Laserlinien-Scanner erfassen nur die geometrischen Abmessungen solcher Bleche und erkennen Welligkeiten, die Aufschluss über Probleme im Prozess geben.