Extrem flexibel und autonom
CNC-gesteuerte Drehautomaten
Im Siemens Schaltwerk in Berlin werden unter anderem Vakuumschaltröhren hergestellt. Zur zerspanenden Bearbeitung der Kontaktstäbe und -scheiben setzt die Vorfertigungsabteilung auf Produktionsdrehautomaten sowie Dreh-Fräszentren inklusive Automation von Index.
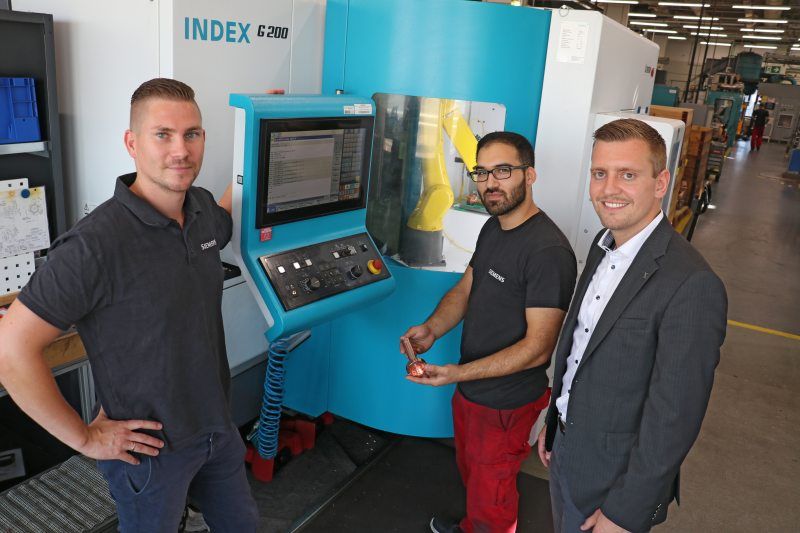
V. l.: Fertigungsbereichsleiter Eric Köhler und Facharbeiter Fatih Ates, Vorfertigung Vakuumschaltröhren bei Siemens, freuen sich mit Index-Gebietsverkaufsleiter Eric Leinung über die gelungenen Arbeitsergebnisse des automatisierten Dreh-Fräszentrums (Bild: Index).
Die Siemens AG ist ein Technologieunternehmen mit Fokus auf die Felder Industrie, Infrastruktur, Mobilität und Gesundheit. Das weitreichende Produktspektrum enthält unter anderem ein durchgängiges Portfolio an Schaltanlagen und Geräten zum Betrieb von Mittelspannungsnetzen, die in unterschiedlichen Anwendungen benötigt werden: in Kraftwerken und Umspannanlagen, in Ortsnetz-, Transformator- oder Übergabestationen, auf Schiffen und in Zügen. Ein Topseller ist die sogenannte Vakuumschalttechnik, die in luftisolierte Schaltanlagen eingebaut wird. Zu deren Kernkomponenten gehören hermetisch dichte Vakuumschaltröhren, wie sie im Berliner Werk entwickelt und hergestellt werden. Der entscheidende Vorteil einer solchen Vakuumschaltröhre ist die über den gesamten Produktlebenszyklus gleichbleibend hohe Qualität, die eine verlässliche und sichere Energieverteilung gewährleistet.
Rolf-Peter Gust ist Abteilungsleiter der Vorfertigung dieser Vakuumschaltröhren am Berliner Standort, wo wichtige Teile ihres Innenlebens produziert werden. Er erklärt: »Wir fertigen hier Kontaktstäbe und -scheiben, die wir zusammen mit anderen zugekauften Komponenten verbauen. Für die hohe Verfügbarkeit und lange Lebensdauer der Vakuumschaltröhren sind vor allem die Kontaktscheiben verantwortlich, für die wir das Material, eine Kupfer-Chrom-Legierung, selbst herstellen. Im Zusammenspiel mit konstruktiven Details sorgt es für hohes Kurzschluss-Schaltvermögen und minimalen Durchgangswiderstand. Kurz gesagt, es macht unsere Vakuumschaltröhren extrem leistungsfähig.«
Qualitätsprodukte entstehen auf Qualitätsmaschinen
Für die zerspanende Bearbeitung dieser Kontaktscheiben und der Kontaktstäbe, von denen jede Vakuumschaltröhre eine feste und eine bewegliche Ausführung enthält, ist Fertigungsbereichsleiter Eric Köhler verantwortlich. Er koordiniert sein Zerspanungsteam und den Maschinenpark, der mit zwölf Produktionsdrehautomaten und Dreh-Fräszentren ausgestattet ist – alle vom deutschen Hersteller Index aus Esslingen: »Wir arbeiten schon sehr lange erfolgreich mit Index zusammen«, erklärt Köhler. »Zwar beziehen wir bei jeder Neuinvestition auch andere Anbieter mit ein, aber letztendlich haben wir uns immer wieder für Index entschieden. Hier bekommen wir die erforderliche Leistungsfähigkeit, gepaart mit einer ›Sinumerik‹-CNC von Siemens, was für uns auch ein entscheidendes Kriterium ist.«
Den Hauptanteil am Produktionsvolumen bestreiten derzeit zwei meist dreischichtig arbeitende Fertigungslinien mit jeweils fünf Maschinen. Diese sind mit Produktionsdrehautomaten »C100« und Dreh-Fräszentren »G160« ausgestattet. »Diese Maschinen ermöglichen uns eine sehr flexible, wirtschaftliche Bearbeitung«, urteilt Köhler, »auch bei unseren nicht einfach zu bearbeitenden Materialien.« Kupfer, aus dem die Kontaktstäbe hergestellt werden, neigt zu langen Spänen, die sich zu Knäuel verbinden und dann den Zerspanungsprozess behindern sowie die Oberflächen beschädigen können. »Hierfür bietet uns Index mit der zyklusintegrierten Spänebruch-Software ›ChipMaster‹ eine sehr praktische Unterstützung«, freut sich Köhler. »Sie optimiert den Spänebruch bei variablem Vorschub.«
Hohe Flexibilität dank autonom arbeitender Maschinen
Eine besonders hohe Flexibilität bieten die beiden autonom arbeitenden Dreh-Fräszentren »G200.2«, die mit der Roboterzelle »iXcenter« ausgestattet sind. »Automatisierung ist für uns eine absolute Notwendigkeit«, ist Köhler fest überzeugt. »Denn erstens gibt es zu wenig Fachkräfte. Obwohl wir selbst ausbilden, klafft da eine Lücke. Zweitens müssen wir wirtschaftlich konkurrenzfähig bleiben, und das klappt nur mit mitarbeiterarmen Schichten.«
Diese Erkenntnis ist in der Vakuumschaltröhrenvorfertigung nicht neu. Die Automatisierung ist dort schon vor vielen Jahren eingezogen. Bereits 2008 statteten die Verantwortlichen ihre damaligen Drehautomaten »C65« mit einem Beladesystem aus, und die heute noch aktiven Dreh-Fräszentren »G160« erhielten vor fünf Jahren Unterstützung von Robotern.
Maschine und Roboterzelle aus einer Hand
Vor fünf Jahren entschlossen sich die Verantwortlichen der Vorfertigung, in besagte Dreh-Fräszentren »G200.2« samt integrierten »iXcentern« zu investieren. Gesucht hatten sie eine Lösung, um Spitzenlasten abfangen und eilige Aufträge zeitnah erledigen zu können. »Unser Bauteilespektrum ist groß. Die Kontaktscheiben unterscheiden sich in Kontur, Dicke und Durchmessern bis zu 40 Millimeter«, erklärt Köhler. »Von den Kontaktstäben fertigen wir 50 bis 60 Varianten aus Stangenmaterial, dazu rund 25 aus unterschiedlichen, vorgefertigten Rohlingen. Hierzu sind Dreh-, Fräs- und Bohrarbeiten erforderlich.«
Für das Dreh-Fräszentrum »G200.2« stellt dieser Umstand kein Problem dar: 65 Millimeter Spindeldurchlass, 165 Millimeter Spannfutterdurchmesser und 660 Millimeter Drehlänge genügen selbst für die großen Kontaktstäbe und ‑scheiben. Die drei Werkzeugträger (jeweils 14 Stationen) mit Y-Achse sind an Haupt- und Gegenspindel einsetzbar.
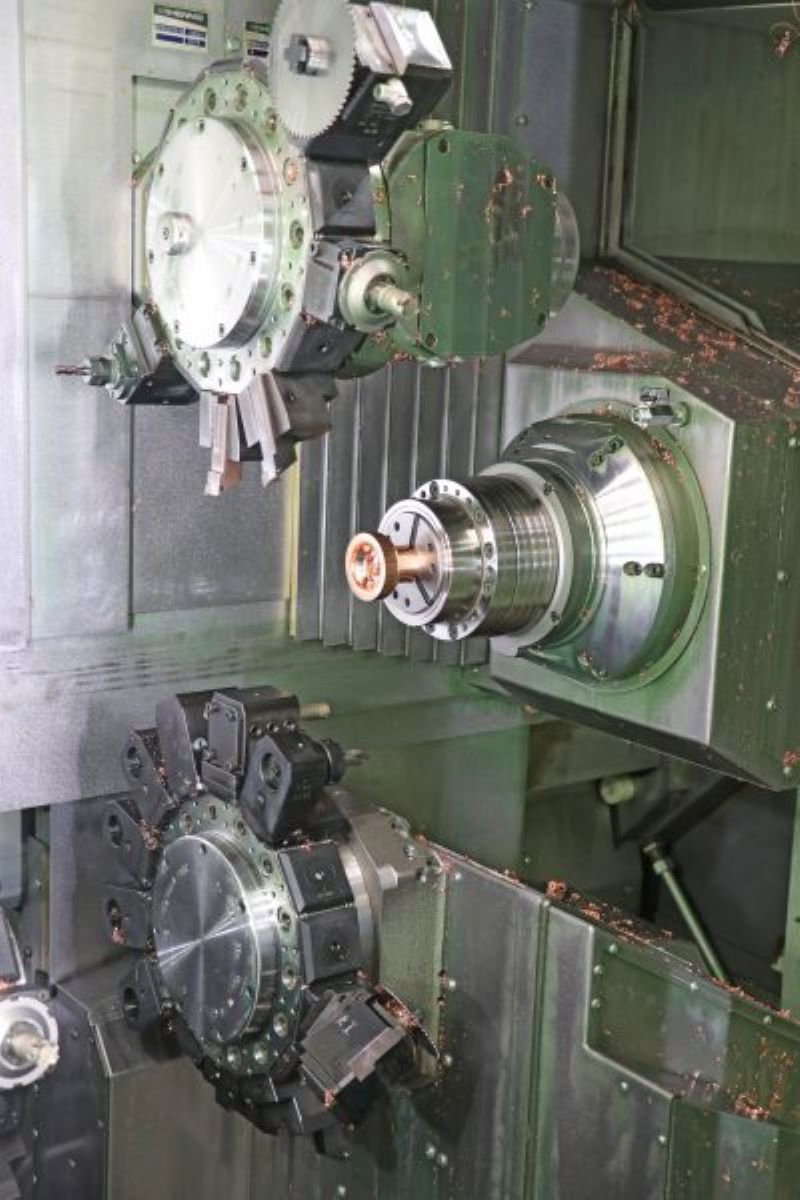
Drei Revolver mit jeweils 14 Werkzeugplätzen plus eine Frässpindel gewährleisten eine wirtschaftliche Komplettbearbeitung (Bild: Index).
Eine Besonderheit ist die leistungsstarke Frässpindel (360 Grad B-Achse, maximal 7200 Umdrehungen pro Minute, 22 Kilowatt, 52 Newtonmeter). Sie gewährleistet anspruchsvolle Bohr- oder Fräsbearbeitungen ohne den Einsatz angetriebener Werkzeughalter. Mit ihrer HSK-A40-Aufnahme bedient sie sich im Pick-up-Verfahren aus dem integrierten Werkzeugmagazin mit sechs Plätzen. Eric Köhler ist begeistert: »Mit der ›G200.2‹ und ihren technischen Fähigkeiten unterbieten wir die bisherigen Prozesszeiten um bis zu 33 Prozent. Außerdem senken wir durch die große Werkzeuganzahl die Rüstzeiten.«
Stundenlanger autonomer Betrieb
Für den autonomen Betrieb des Dreh-Fräszentrums sorgt die installierte Automatisierung, die ganz nach Bedarf eingesetzt werden kann. Denn die »G200.2« ist nicht nur mit erwähntem »iXcenter« ausgestattet, sie verfügt zusätzlich über einen Kurzstangenladeautomaten und eine integrierte Portalabnahmeeinrichtung mit Transportband.
Die Roboterzelle »iXcenter« ist dabei an die Maschine angedockt. Sie kann während des Rüstvorgangs einfach verschoben werden und erlaubt so einen ungehinderten Zugang zum Arbeitsraum. Im Produktionsbetrieb wird die Zelle vor dem Maschinenarbeitsraum fixiert. Zugang zum Arbeitsraum der Maschine erhält der 6-Achsen-Roboter über die Schiebehaube der Maschine, die sich hinter der Roboterzelle automatisch öffnet. Zu beliebigen Zeitpunkten kann das Bedienpersonal ohne Produktionsunterbrechung den Vertikalspeicher im oberen Speicherbereich mit Rohteilpaletten beladen und die Paletten mit Fertigteilen aus dem unteren Speicherbereich entnehmen.
Eric Köhler und seine Kollegen waren schnell von diesem Konzept überzeugt, sodass sie schließlich zu den ersten »iXcenter«-Kunden gehörten. »Wir haben von Anfang an sehr positive Erfahrungen gemacht«, bestätigt der Fertigungsbereichsleiter. »Allerdings sind die sieben Kilogramm maximale Traglast des Roboters etwas knapp bemessen, sodass wir am Überlegen sind, diesen gegen einen Roboter mit zwölf Kilogramm auszutauschen.«
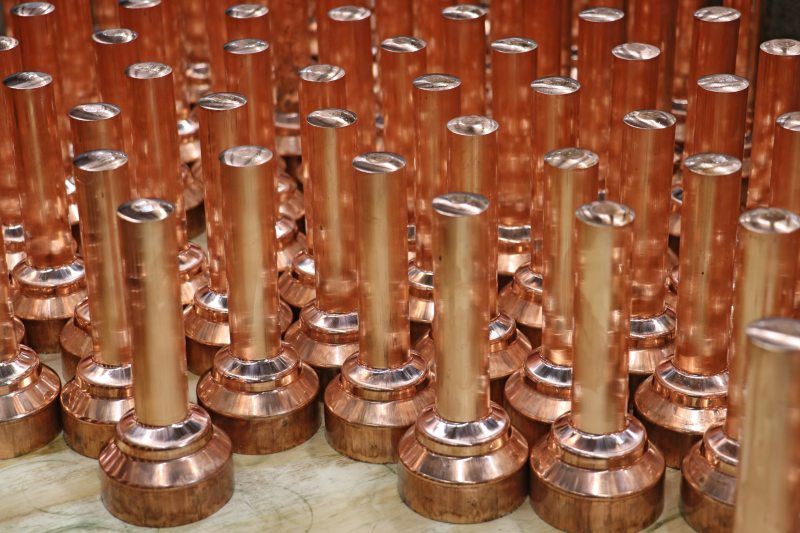
Für größere Kontaktstäbe werden vorgeformte Kupferrohlinge eingesetzt (Bild: Index).
Er weist noch darauf hin, dass die Anzahl der einsetzbaren Paletten von der Bauteilgröße abhängt. »Aus Sicht des autonomen Betriebs ist es ideal, wenn wir kleine Kontaktstäbe aus Stangenmaterial fertigen und diese dann mittels Roboter im Palettenmagazin ablegen. So können wir acht bis zwölf autonome Betriebsstunden erreichen. Bei größeren Kontaktstäben, die wir aus vorgeformten Rohlingen herstellen, lassen sich für Roh- und Fertigteile nur jeweils vier oder fünf Paletten mit je zwölf Plätzen einsetzen. Damit liegen wir bei guten vier Stunden bedienerfreiem Betrieb.«
Eine weitere Möglichkeit ist, den Roboter für Einlegeteile zu nutzen und die Fertigteile mittels Abnahmeeinrichtung und Transportband aus der Maschine zu befördern. »Mehr Flexibilität geht nicht«, schließt Eric Köhler.