EHLA-Versuchsanlage
3D-Druck/additive Fertigung
Das Fraunhofer ILT optimiert die Fertigung von Bipolarplatten durch ein Hochgeschwindigkeits-Laserauftragschweißverfahren. Statt teurer Frästechnik werden verschleißfeste Schichten auf günstigen Baustahl aufgetragen, was Kosten, Bauzeit und Werkzeugverschleiß reduziert. Der Prozess ermöglicht zudem effiziente Reparaturen und verbessert die Verschleißbeständigkeit.
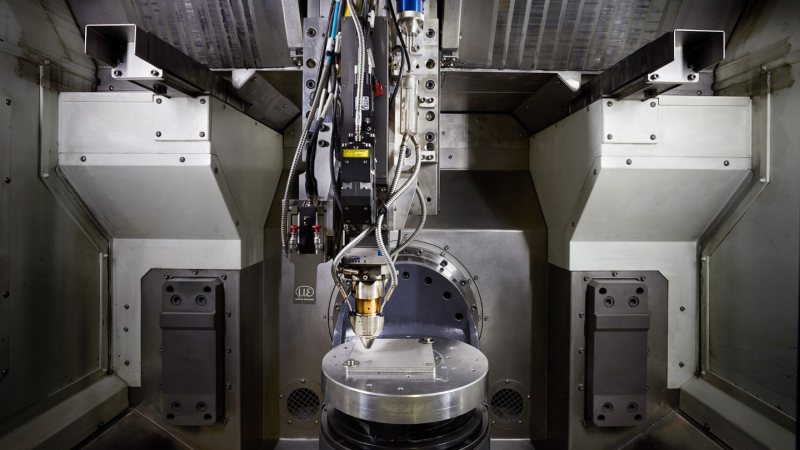
Versuchsanlage im H2Go-Projekt: Auf einer EHLA-Anlage werden Bauteile für Brennstoffzellen schnell und präzise mit Verschleißschutzschichten beschichtet (Bild: Fraunhofer ILT).
Die Großserienfertigung von Bipolarplatten für Brennstoffzellen erfolgt im Sekundentakt. Um eingesetzte Umformwerkzeuge vor Verschleiß zu schützen, werden sie bisher stundenlang aus hochwertigen Metalllegierungen gefräst. Im Gegensatz hierzu bringt das Fraunhofer-Institut für Lasertechnik ILT in Aachen im Rahmen des nationalen Aktionsplans Brennstoffzellenproduktion (H2Go) mithilfe des extremen Hochgeschwindigkeits-Laserauftragschweißens (EHLA) verschleißfeste Funktionsschichten endkonturnah auf günstigen Baustahl auf. Die Kosten, Bauzeit und der Verschleiß der Werkzeuge sinken dabei signifikant. Zudem ist der Prozess auch zur Reparatur beschädigter und verschlissener Werkzeuge nutzbar.
Additives Verfahren
Auf Basis digitaler Prozessketten lassen sich die verschleißfesten Funktionsschichten mit dem additiven Verfahren schnell und effizient aufbringen. Der 3D-Materialaufbau lässt sich zudem so exakt steuern, dass die auf kostengünstigen Baustahl aufgeschweißte, besonders verschleißfeste Schicht der beabsichtigten Endkontur sehr nahekommt. Statt diese in einem stundenlangen, werkzeugintensiven Prozess aus dem Vollen zu fräsen, muss das Umformwerkzeug also nur noch gezielt endbearbeitet werden. EHLA minimiert daher die Fertigungszeit und -kosten, da nur noch eine dünne Funktionsschicht aus hochwertigem Material aufgebracht und endbearbeitet werden muss.
Als Beschichtungsmaterialien dienen in dem Forschungsprojekt Schnellarbeitsstahl 1.3343 und die martensitische Edelstahllegierung Ferro55. 1.3343 erreicht eine Härte von etwa 830 HV0,5 und Ferro55 etwa 820 HV0,5. Damit liegen sie etwa im Bereich des üblichen Werkzeugstahls 1.2379. Der Verschleißschutz lässt sich mit der Beschichtungsgeschwindigkeit von 30 m/min auftragen. Pro Lage wird eine Schichtdicke von ca. 1,2 mm erzielt. Durch mehrlagigen Auftrag kann die geforderte Schichtdicke eingestellt werden. Die digitale Steuerung gewährleistet einen präzisen und selektiven Materialaufbau, der es erlaubt, robuste Verschleißschutzschichten herzustellen. Deren Struktur ist nach Erkenntnissen des Instituts für den Verschleißschutz wichtiger als die Härte des Werkstoffs, denn die Verschleißbeständigkeit hänge in sehr hohem Maß vom Gefügezustand des Materials ab. Dank extrem feinkörniger Mikrostrukturen würden sich die mechanischen Eigenschaften verbessern und so der Abrieb deutlich verringern. Die feinkörnige Struktur verleihe den Schichten auch bei starker Belastung eine hohe Beständigkeit gegen Abnutzung.
Um die Verschleißbeständigkeit präzise zu bewerten, setzt das Institut einen Gleitreibverschleißtest der TU Clausthal ein, der realistische Abnutzungsszenarien für den Anwendungsfall simuliert. Laut eigener Angabe deuten die bisherigen Ergebnisse auf signifikante Vorteile der per EHLA beschichteten Testkörper gegenüber herkömmlichen Werkstoffen hin.