Für den perfekten Ritt
CNC-gesteuerte Fräsmaschinen
Wer ein »Thunderbike« sieht, ist erst einmal sprachlos. Der Harley-Davidson-Händler und Custombike-Hersteller verrät, wie er individuelle Kupplungsdeckel und Felgen fertigt und welche Rolle die Mill-Turn-Technologie von Hermle dabei spielt.
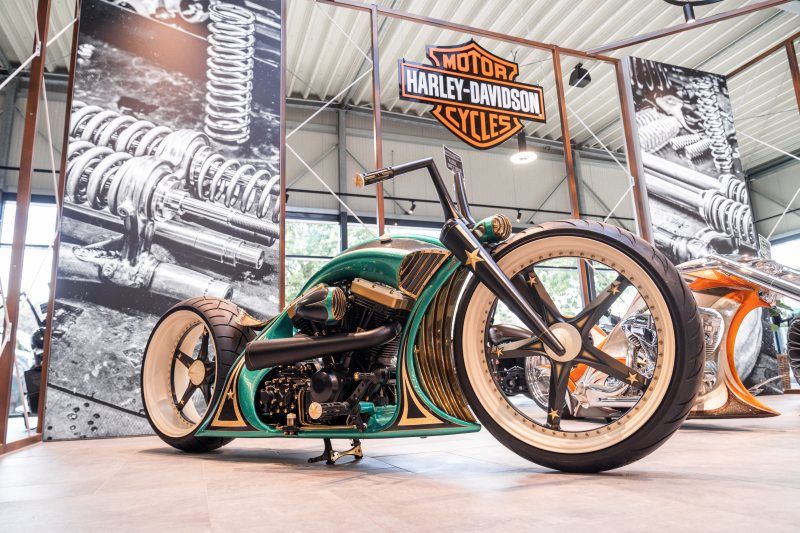
Thunderbike ist weltweit für seine Custombikes bekannt. Mit der »Open Mind« holte das Unternehmen 2008 den Europameistertitel nach Hamminkeln (Bild: Hermle).
»Wir sind wirklich ein Stück von der Scheibe zurückgegangen«, erinnert sich Thomas Zarmann, Produktionsleiter bei Thunderbike, als sein Kollege Herbert Niehues das erste Mal einen 300-Kilogramm-Rohling auf dem Bearbeitungszentrum »C 42 U MT« mit 800 Umdrehungen pro Minute rotieren ließ. Die Szene ereignete sich 2013, nachdem das Unternehmen sein erstes Bearbeitungszentrum der Maschinenfabrik Berthold Hermle AG in Betrieb nahm.
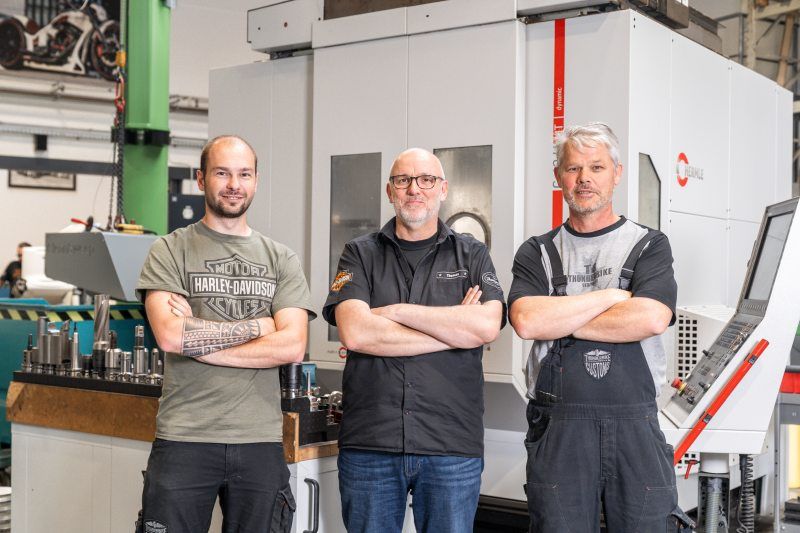
Von links: Maschinenbediener Julian Otten, Produktionsleiter Thomas Zarmann und Maschinenbediener Herbert Niehues (Bild: Hermle).
Die Sorge vor dem ersten Anlauf war unbegründet, denn Hermle hat die Mill-Turn-Varianten nach den Sicherheitsanforderungen für Drehmaschinen entwickelt. Das betrifft zum Beispiel die Einhausung und Dimensionierung der kompletten Verkleidungen inklusive Maschinendach. Zudem ist ein Wuchtsystem in den Drehtisch integriert. Es berücksichtigt Massenträgheitsmomente und wuchtet selbst die 300-Kilogramm-Rohlinge – für einen sicheren Betrieb auch bei Höchstdrehzahlen.
Thunderbike ist ein 160 Personen starkes Unternehmen im nordrhein-westfälischen Hamminkeln und bietet Motorräder von Harley-Davidson sowie Custombikes an, für die das Unternehmen heute weltweit bekannt ist. In Hamminkeln produziert der Betrieb eigene Teile für das Customizing von Motorrädern bis hin zu kompletten Custombikes mit eigenen Rahmen. Eine Servicewerkstatt gehört ebenso dazu wie ein moderner Showroom und der Vertrieb von Original-Harley-Davidson- und Aftermarket-Artikeln.
Mill-Turn-Technologie
Produktionsleiter Zarmann erläutert das Wie und Warum rund um die Investition in die Hermle-Maschinen, von denen Thunderbike mittlerweile drei besitzt. Die Ansprüche an Oberflächen und Design sowie der Ehrgeiz weiterzukommen, weckten 2012 den Bedarf nach einer neuen Maschine. Der Maschinenbauer aus Gosheim war damals der einzige Hersteller, der die passende Technologie für das bieten konnte, was Thunderbike vorhatte: filigran anmutende Felgen aus dem Vollen fräsen, in einer bis dahin unerreichten Perfektion.
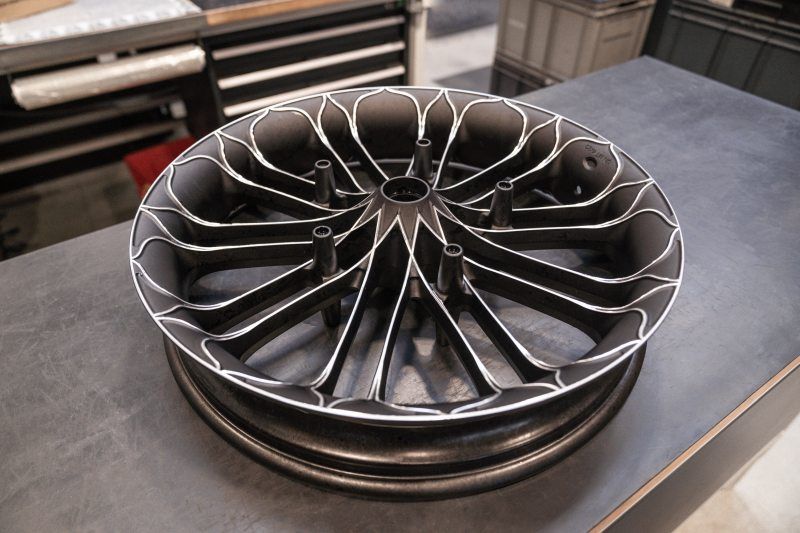
Nach dem Eloxieren der Monoblockfelge werden zum Beispiel noch einzelne Details wieder freigefräst, die das Design betonen (Bild: Hermle).
»Schon damals stellten wir unsere eigenen Felgen her. Nur brauchten wir dafür drei Maschinen und fünf bis sechs Aufspannungen. Das Rad hatte auch von der Optik und von der Qualität nichts mit dem zu tun, was wir heute machen«, verdeutlicht Zarmann.
Der zugleich dreh- und schwenkbare Tisch ermöglicht das Drehen in unterschiedlichen Winkeln. Im Gegensatz zur reinen Drehmaschine können somit kürzere Werkzeuge eingesetzt und komplexe Geometrien realisiert werden.
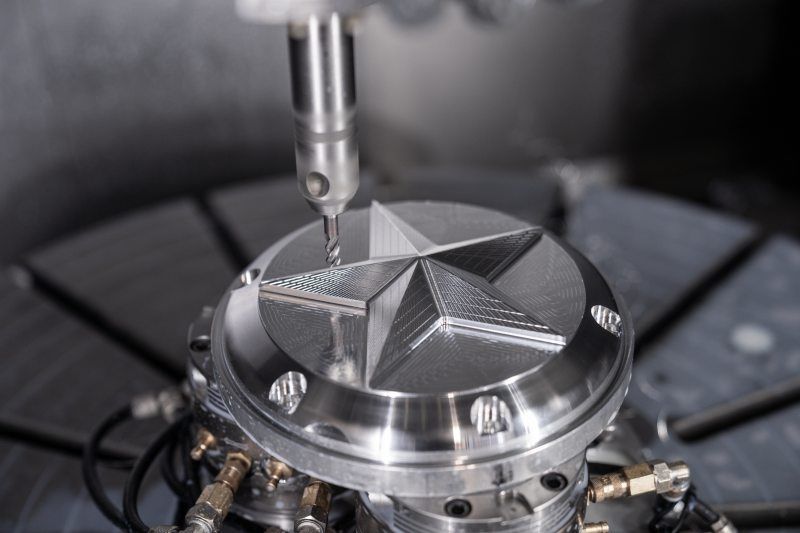
Das Bearbeitungszentrum »C 42 U MT« fräst in nur wenigen Minuten den Deckel mit Stern aus dem Rohling (Bild: Hermle).
»Die ›C 42 U MT‹ war in puncto Technologie und Platzangebot genau das, was wir 2012 gebraucht haben.« Bis heute meistere sie die größten Herausforderungen – die Monoblock-Räder – problemlos: lange Laufzeiten zwischen zehn und 20 Stunden bei hohen Vorschüben und Drehzahlen und fast immer im 5-Achs-Simultanmodus. Am Ende muss die Oberfläche perfekt sein.
Verstärkung kam in den Jahren 2016 und 2020 in Form zweier »C 32 U«, die zwei vorhandene Fremdmaschinen ersetzten. »Warum die nächste Maschine auch eine Hermle war? Bei der ersten Anlage haben uns die Zuverlässigkeit und Präzision sowie die Ergonomie und das Bedienkonzept überzeugt. Hinzu kam der vorbildliche Service: Die Monteure sind einfach fit – egal, ob ein Kabel lose ist oder ein mechanisches Problem vorliegt«, begründet Zarmann. Neben den Kosten für die Reparatur ist für ihn Stillstand das Schlimmste.
Universal einsetzbar
15 bis 20 Prozent der Frästeile müssen auf die »C 42 U MT« zum Fräsen und Drehen. »Aber wir lassen die Maschine ja nicht stehen, nur weil wir gerade keine Teile haben, die rund sind. Wir können darauf ja alle Frästeile laufen lassen«, sagt der Produktionsleiter. Die drei Bearbeitungszentren schafften Kapazität und das einheitliche Bedienkonzept bedeute Flexibilität. »Wir haben jetzt mehrere Maschinen, auf denen wir einen Großteil unserer Frästeile einfach direkt hin- und herschieben können. Damit sind wir immer in der Lage zu produzieren.«
Der Betrieb fertigt neben den Felgen auch Anbauteile wie Radsterne, Blinker- und Luftfiltergehäuse, meist aus Aluminium, Messing und manchmal aus Edelstahl. Letzterer kommt zum Beispiel bei den Air-Ride-Zylindern für die Luftfahrwerke zum Einsatz. Obwohl die Zylinder reine Drehteile sind, werden sie auch mal auf dem Fräs-Drehzentrum bearbeitet, wenn alle Drehbänke belegt sind. »Wir versuchen, die Produktion so flexibel wie möglich zu gestalten. Das vereinfacht uns den Alltag«, sagt Zarmann.
Ein weiteres Teil, das auf der 5-Achs-Fräs-Drehmaschine Späne lassen muss, ist der selbst designte Kupplungsdeckel »Open Mind«. Anhand der beliebten Stern-Designvariante erklärt Zarmann den Entstehungsprozess.
Den ersten Schritt macht 3D-Produktdesigner und Konstrukteur André Kosthorst: An seinem Rechner entwirft er die Idee und übersetzt mithilfe eines 3D-Druckers seine digitale Zeichnung in einen ersten Prototyp. Stimmt alles, muss das Team entscheiden: Welche Maschine soll das Teil fräsen und mit welchem Spannmittel? »Da ist natürlich die Erfahrung von den Kollegen gefragt«, betont Zarmann und zeigt in Richtung der Zerspanungsabteilung, die im Erdgeschoss schräg unterhalb des Sozialraums liegt. Eine Simulationssoftware überprüft die Programmierung für das Fräs-Drehzentrum, dann spannt Herbert Niehues den ersten Rohling auf. »Ich arbeitete bereits Ende der 1990er-Jahre auf einer der ersten Hermle-Maschinen der ›C-Reihe‹. Ihre ergonomische Bedienbarkeit, das intuitive Steuerungskonzept und ihre hohe Funktionalität überzeugen – damals wie heute«, erläutert er dabei.
Nach wenigen Minuten ist bereits der Stern zu erkennen. Der Oberfläche sind die Frässpuren anzusehen. Diese zu beseitigen, ist Aufgabe der Kollegen in der Oberflächenbearbeitung. Sie schleifen und sandstrahlen den unfertigen Kupplungsdeckel. »Wir könnten natürlich den Deckel auf der Maschine mit einer so perfekten Oberfläche fertigen, dass wir nicht mehr Hand anlegen müssten. Das kostet aber Zeit, und wir würden statt der 50 nur sieben Teile pro Tag schaffen«, erläutert Zarmann. Die schwarze Farbe erhält die Komponente beim Eloxieren. Ein abschließender Gang durch eines der drei 5-Achs-Bearbeitungszentren bringt den Stern schließlich zum Glänzen.
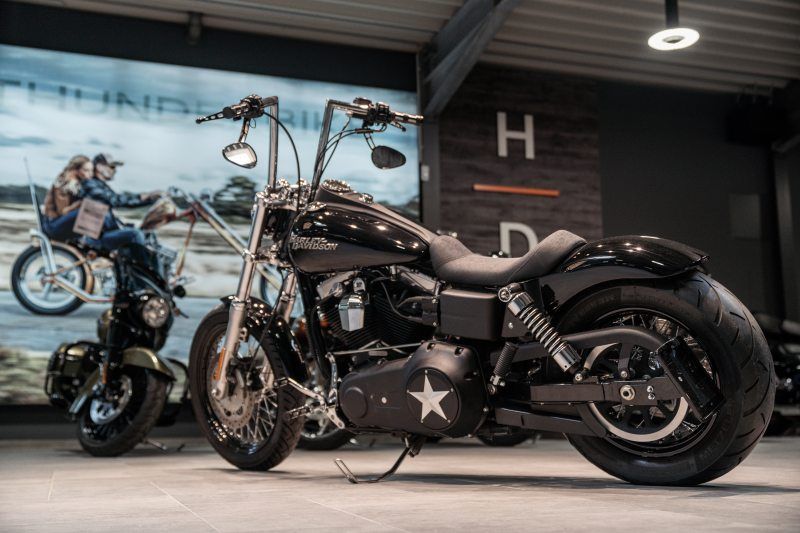
Der verzierte Deckel wertet das schwarze Bike optisch auf (Bild: Hermle).
Der schwarze Kupplungsdeckel ist für ein schwarzes Bike bestimmt, an dem auch der blank gefräste Stern entsprechend zur Geltung kommt. Nach dem letzten Span bleibt das rohe Aluminium ungeschützt. »Wer damit zwei Jahre durch den Regen fährt und nie putzt, dem fängt der Stern an zu blühen«, warnt Thomas Zarmann. »Aber die meisten, die in solche Designteile investieren, pflegen ihre Fahrzeuge entsprechend. Bei Regen bleiben die meisten Harleys sowieso in der Garage.«