Pilotanlage für Hairpin-Statoren
Bearbeitungszentren
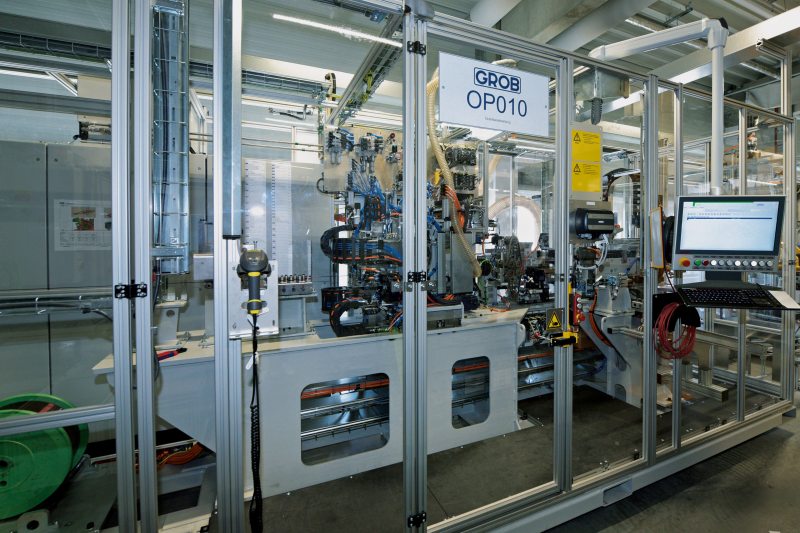
Mit der Pilotanlage lassen sich Prozesse für die Serienproduktion abbilden und optimieren (Bild: Grob).
Die Berliner Bosch-Tochter eAx solutions ist ein Entwicklungsdienstleister, der sich unter anderem mit der Entwicklung und Industrialisierung von elektrischen Achslösungen beschäftigt. Das Unternehmen entwirft und verkauft Entwicklungsprojekte, zu denen auch Prototypen gehören. Zu den Aufgabenstellungen gehören auch Prozesse, die Großserie so weiterzuentwickeln, dass sich ein Großserienlauf mit kleinstmöglichem Risiko umsetzen lässt. Um derart robuste Projekte darstellen zu können, wurde eine Pilotfertigung installiert, mit der man in der Lage ist, Prozesse in Großserie zu entwickeln: von der Produktion des Stators, des Rotors, der verschiedenen Montageprozesse und der Elektronik bis hin zum Test.
Flexible Produktionslinie
Im Zuge einer Achsentwicklung hat sich der Betrieb für die Beschaffung einer sehr flexiblen Produktionslinie von Grob zur Fertigung der Statoren und der Endmontage entschieden. Die Linie bietet besondere Flexibilität, sodass sowohl in der Höhe als auch im Durchmesser verschiedene Produktvarianten gefertigt werden können − mit kurzen Rüstzeiten für neue Kunden. Der Linienhersteller lieferte zudem einen Simultaneous Engineering Support von der Auslegung des Produkts bis hin zur integrierten Produkt- und Prozessgestaltung.
Mit der Pilotanlage werden in Berlin zum einen Hairpin-Statoren produziert, zum anderen Getriebe montiert sowie die Endmontage der elektrischen Achsen durchgeführt und getestet. In der ersten Station wird Isolationspapier in ein Blechpaket eingeführt. Danach wird in weiteren Stationen der Draht zum Biegen vorbereitet, indem er gerichtet und abisoliert wird. Durch mehrere Umformprozesse wird der Draht anschließend in die finale Hairpin-Form gebracht. Diese Pins werden in einer Vorrichtung nach einem bestimmten Wickelschema sortiert, um dann in das Blechpaket eingeführt zu werden. Jetzt werden die Pins geweitet und geschränkt, eine Schweißschablone aufgesetzt und die Pins auf gleiche Länge geschnitten. Durch Laserschweißen werden die Pins verbunden und anschließend imprägniert. Der Stator und der Rotor werden dann mit dem Systemgehäuse »verheiratet« und mit dem Getriebe sowie dem Inverter auf der Anlage zusammengebaut. Diese Electric Drive Unit (EDU) wird schließlich im End-of-Line-Prüfstand getestet. Die Anlage hat eine Taktzeit von 1200 Sekunden und ist auf 5000 Einheiten im Jahr ausgelegt.