Automation clever integriert
Fräsmaschinen allgemein
Seit Juni 2021 laufen bei Hamilton zwei CNC-Kompaktbearbeitungszentren mit Roboterautomation von Hermle. Teamleiter Luca Morell ist vom hohen Integrationsgrad der Lösung begeistert − und von einem Partner, der die technischen Probleme versteht und seine Versprechen hält.
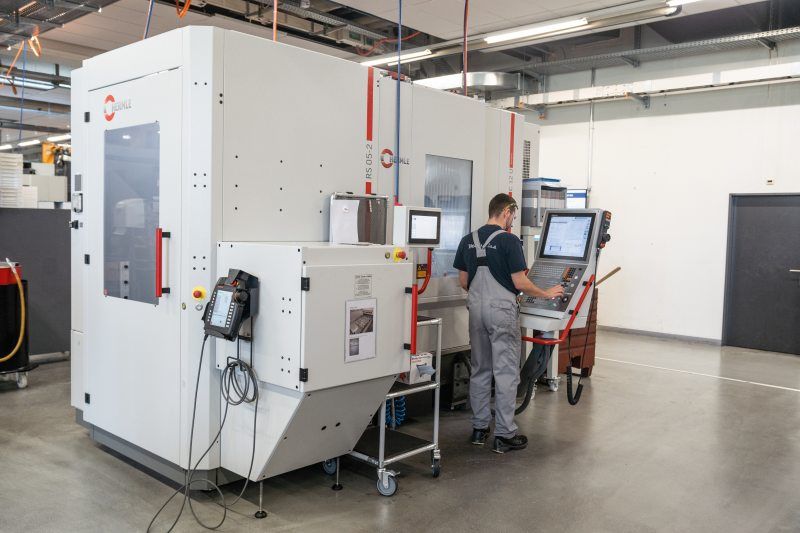
Das kompakte CNC-Bearbeitungszentrum mit Robotersystem bietet hohe Produktivität auf kleinem Raum (Bild: Hermle).
Einatmen, ausatmen – so selbstverständlich diese Funktion für den Körper ist, so kompliziert ist es, dies einer Maschine beizubringen. Setzt der Atemreflex aus, hängt die lebensnotwendige Sauerstoffversorgung an O2-Grenzwerten, Atemminuten, -zugvolumina und -frequenzen sowie Druckeinstellungen. Wie genau, das weiß das Unternehmen Hamilton, das an den Hauptstandorten in Bonaduz und Domat/Ems in der Schweiz Beatmungsgeräte, Pipettierroboter, Biopharmasensoren, Probenverwaltungssysteme sowie weitere Produkte entwickelt und herstellt.
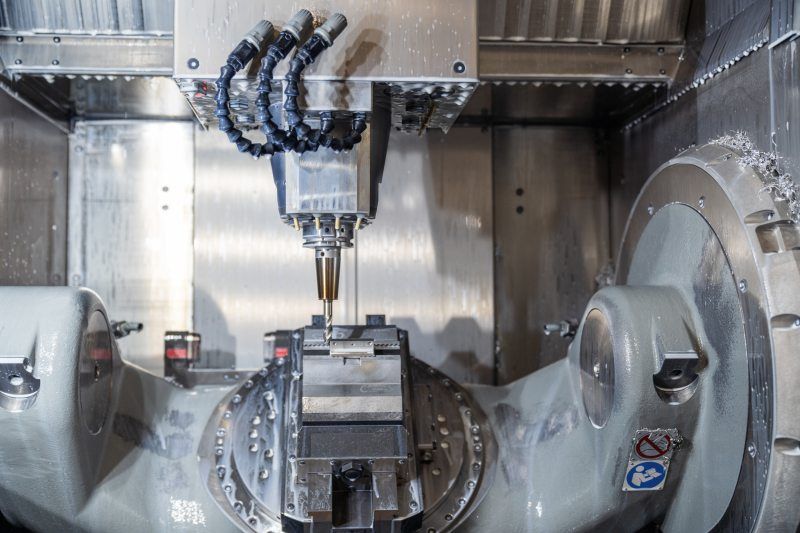
Hamilton ersetzte drei Stand-alone-Maschinen durch zwei effizientere Bearbeitungszentren mit Automation (Bild: Hermle).
Das Familienunternehmen setzt auf eine hohe Fertigungstiefe, um unabhängig zu sein und den hohen Qualitätsansprüchen an medizinische Geräte gerecht zu werden, wie Luca Morell erklärt. Der Teamleiter in der mechanischen Produktion bei Hamilton steht zwischen zwei neuen 5-Achs-Bearbeitungszentren vom Typ »C 12 U« der Maschinenfabrik Berthold Hermle AG. Automatisiert sind beide Anlagen jeweils mit der zweiten Generation des kompakten Robotersystems »RS 05-2«. Hinter ihm arbeiten kontinuierlich zwei weitere Bearbeitungszentren der »High-Performance-Line«: eine »C 32 U« sowie eine »C 42 U«, die hauptzeitparallel gerüstet wird.
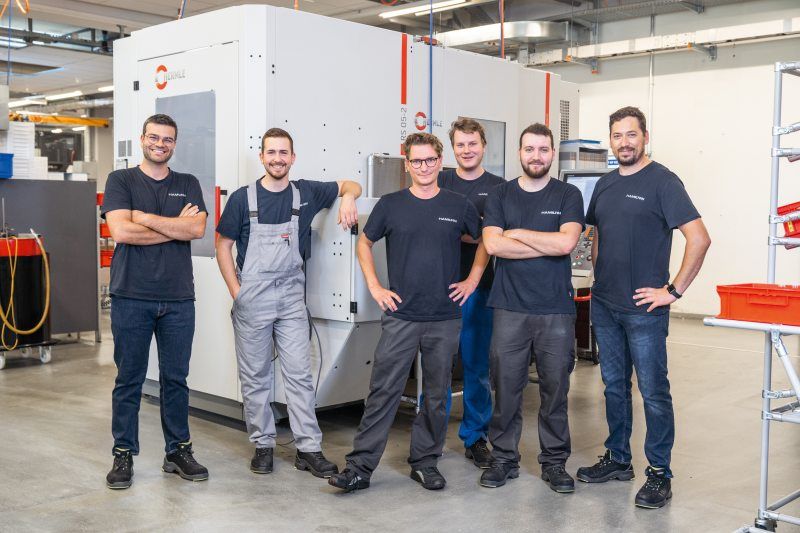
Luca Morell (li.) und sein Team sind froh über das hohe Potenzial der automatisierten Bearbeitungszentren (Bild: Hermle).
Gestiegene Nachfrage
»Als vor circa eineinhalb Jahren unsere Auftragslast durch die Decke schoss, wurde deutlich, dass wir mit dem damaligen Maschinenbestand das hohe Auftragsvolumen nicht mehr bewerkstelligen konnten. Da wussten wir: Der richtige Zeitpunkt war gekommen, um zu investieren«, erzählt Morell. Der Wunsch war, drei Stand-alone-Maschinen durch effizientere Anlagen mit Automation zu ersetzen. Dabei war ein automatisierter Schraubstock Pflicht. »Wir wollten unterschiedlich große Teile auch in Geisterschichten rüsten, bearbeiten, wechseln und wenden können«, erläutert Morell. Der Anspruch an den eigentlichen Fräsprozess war ebenso hoch: Hamilton erwartet höchstmögliche Form- und Lagetoleranzen trotz der dünnwandigen und fragilen Bauteilgeometrien.
Mit dem Gosheimer Maschinenbauer wurde bereits vor rund zwei Jahren das erste Mal zusammengearbeitet. Damals zogen schließlich die Bearbeitungszentren »C 42 U« sowie »C 32 U«, beide mit »HS flex«-Handlingsystem, in die Metallbearbeitung in Bonaduz ein. Ihre 5-Achs-Technologie steigerte für den Gerätehersteller die machbare Komplexität der zu fertigenden Bauteile deutlich. »In puncto Performance und Genauigkeit hat uns Hermle bereits mit diesen beiden Fräszentren überzeugt. Ausschlaggebend für die erneute Investition waren die Durchgängigkeit der Automationslösung und die Qualität der Zusammenarbeit«, erzählt Morell. »Von Anfang an wurden wir auch in technischer Sicht verstanden und umfassend betreut.«
Doppelt fräst besser
Die Lösung, die seit Juni 2021 in Bonaduz in Betrieb ist, besteht aus zwei »C 12 U«-Bearbeitungszentren jeweils mit Robotersystem »RS 05-2«. Dass die Anlagen sehr kompakt sind und trotz Automation nur wenig Platz benötigen, sprach zusätzlich für sie. Die Teilebevorratung und -versorgung erfolgt über einen Schubladenspeicher. »Neben Prototypen haben wir auch Standardteile eingerichtet, von denen wir pro Jahr etwa 4000 Stück bearbeiten müssen. Sie liegen in einer der fünf Schubladen bereit, falls die Kleinserien- oder Prototypenlast nicht so groß ist. Sobald Luft ist, plant das System sie automatisch in die Fertigung ein«, erläutert Morell.
Mit dieser Grundlast, wie sie der Teamleiter nennt, deckt Hamilton rein rechnerisch über 13 Stunden Bearbeitungszeit ab: In der Matrize sitzen 78 Teile, die in knapp zehn Minuten fertig bearbeitet sind. Weitere fünf Stunden können über die Einzelteile in den vier anderen Schubladen verplant werden. »Wenn die Anlage fertig eingerichtet ist, brauchen wir lediglich zwei Stunden personellen Aufwand, um sie 18 Stunden autark arbeiten zu lassen. Wir erreichen somit einen enormen Nutzungsgrad«, freut sich der Teamleiter.
Greifer wechselt sich
So lange Autarkzeiten bei Rohlingen mit Längen zwischen 20 und 150 Millimetern ermöglicht der Greiferbahnhof in der Roboterzelle, der Platz für acht Greiferpaare bietet. Hamilton hat sich bewusst gegen einen einzelnen NC-Greifer und für die pneumatischen Varianten entschieden »Ein Greifer mit Stellmotor braucht deutlich länger, bis er das korrekte Teilemaß erreicht hat. Die pneumatische Variante dagegen hat zwar einen eingeschränkteren Greifbereich, dafür ist sie schneller. So sparen wir wertvolle Zeit«, erklärt Morell. Der Roboter wechselt automatisch die Greifer und ermöglicht so den Teilewechsel auch in den personenlosen Schichten.
Nicht nur die Möglichkeiten der Automation begeistern Luca Morell, sondern auch die Bedienbarkeit. »Anfangs sorgten wir uns, ob ein Robotersystem mit seinen sechs Achsen nicht zu komplex wäre. Mit dem ›Hermle-Automation-Control-System (HACS)‹ erwies sich diese Angst jedoch als unbegründet.« Es nimmt das Bedienpersonal quasi an die Hand und führt durch die notwendigen Programmierschritte. Das Roboterhandling wirkt oberflächlich betrachtet sehr simpel: Der Roboter nimmt ein Teil aus der Matrize und platziert es im Schraubstock. Nachdem die Bearbeitung beendet ist, entnimmt er es wieder und legt es zurück in den Teilespeicher.
Zwei Monate vor Auslieferung der Anlagen bemerkten Morell und sein Team, dass sie bei den Prozessschritten eine Sache übersehen hatten: Einige Bauteile müssen anders in der Matrize liegen, als sie im Schraubstock eingespannt sind. Um sie bestmöglich bearbeiten zu können, bräuchte es eine Drehung um 90 Grad. »Von der mechanischen Seite her ist das Wenden einfach. Wir wussten jedoch nicht, wie wir das programmiertechnisch mit dem Roboter umsetzen konnten.« Die Befürchtung, einen Robotertechniker kommen zu lassen oder doch eine Drittsoftware installieren zu müssen, konnte Hermle ihm nehmen: »Sobald wir das Problem erläutert hatten, setzten sich die Experten in Gosheim daran, die Drehung des Robotergreifers in die ›HACS‹-Software zu integrieren«, erinnert sich Morell. Später zeigte sich: »Das Ergebnis hat sofort funktioniert.«
Aus Respekt wurde Faszination
Als ebenso kompetent beschreibt der Teamleiter die Service- und Anwendungstechniker. »Sowohl bei der Inbetriebnahme als auch bei der Einarbeitung überzeugte das Hermle-Team mit seinem Fachwissen und Können.« Maschinenbediener Fadri Pitsch erzählt, dass er anfangs schon Respekt vor dem Roboter gehabt habe. »Nach der Einarbeitung ging es aber problemlos.« Heute arbeitet er sehr gerne am »C 12 U«-Bearbeitungszentrum, auch wegen des Roboters. »Die Technologie fasziniert«, schwärmt er.
Insgesamt arbeiteten bis Jahresende zwei CNC-Programmierer und vier Maschinenbediener an den neuen Anlagen, was an dem hohen Initialaufwand lag, wie Morell erklärt: »Wir hatten extra die Manpower erhöht, damit wir möglichst schnell die Teile, die auf den drei vorherigen Maschinen gefertigt wurden, umprogrammieren und auf den neuen Bearbeitungszentren einfahren konnten. Jetzt brauchen wir nur noch zwei Personenstunden für den 24-Stunden-Dauerlauf und können das volle Potenzial der automatisierten Anlagen ausschöpfen«, sagt Morell. Wie hoch das ist, kann er nur schätzen und nennt eine Produktivitätssteigerung von 25 bis 30 Prozent im Vergleich zu den drei vorherigen Maschinen.