Antriebe mit Feingefühl
Antriebe
Hochwertige mechanische Uhren sind edle Schmuckstücke mit einem komplexen Innenleben. Um sie herzustellen, müssen zahllose Arbeitsschritte präzise ineinandergreifen. Heute gibt es dafür Montagestationen, die die Uhrmacher mit automatisierten Abläufen unterstützen. Beim Transport während der Montage sorgt ausgewählte Antriebstechnik von Faulhaber für das notwendige Feingefühl, damit die filigranen Uhrwerke keinen Schaden nehmen.
Diesen und viele weitere Fachbeiträge lesen Sie in der 2020er-Ausgabe des Jahresmagazins »Maschinenbau + Metallbearbeitung«, das Sie über diesen Link bestellen können.
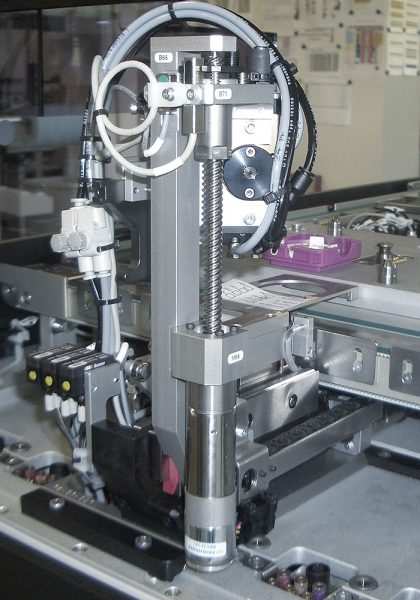
Im Verhältnis zu den kleinen Dimensionen müssen beträchtliche Wege zurückgelegt werden. Der vertikale Hub des Laders etwa beträgt gut 20 Zentimeter (Bild: Precitrame).
Die Grundlage für mechanische Uhrwerke liefert eine hochentwickelte Handwerkskunst, die vor allem in der Schweiz über Jahrhunderte von Generation zu Generation weitergegeben wurde. Allerdings fertigen die meisten Hersteller ihre Produkte heute in Stückzahlen, die sich in reiner Handarbeit nicht mehr bewältigen lassen. Zwar werden weiterhin die wichtigen Arbeitsschritte durchweg von Hand ausgeführt, der gesamte Ablauf ist jedoch arbeitsteilig in verschiedene Prozesse unterteilt und die Facharbeiter werden maschinell unterstützt, zum Beispiel mit automatischen Fördereinrichtungen, die den Montageablauf deutlich erleichtern. Ein gutes Beispiel dafür liefert die Montagestation von Precitrame. Das Schweizer Unternehmen, das auf Rundtakt-Transfer- und Finishing-Anlagen für feinmechanische Produkte spezialisiert ist, hat diese Station speziell für die halbautomatische Fertigung hochwertiger Uhren entwickelt.
Montagefabrik im Mini-Format
Bei geschlossenem Maschinengehäuse sieht man nicht viel vom technischen Innenleben der Montagestation. In der Mitte der Arbeitsfläche ist vorne lediglich eine kleine runde Aussparung sichtbar. Hierhin bekommt der Uhrmacher das Uhrwerk angeliefert, um den nächsten Montageschritt auszuführen. Ist dieser beendet, legt er es dort wieder ab. Das Werkstück wird nun unter der Abdeckung weitertransportiert, während der Mitarbeiter das nächste zur Bearbeitung bekommt. Unter der Abdeckung stecken unterschiedliche Fördereinrichtungen, die wie die Miniaturversion einer Montagefabrik aussehen. Die Werkstücke fahren auf zahlreichen nebeneinanderliegenden Förderbändern hin und her, passieren Weichen und können ganz unterschiedliche Wege nehmen, je nachdem welcher Arbeitsschritt am Los gerade durchgeführt wird.
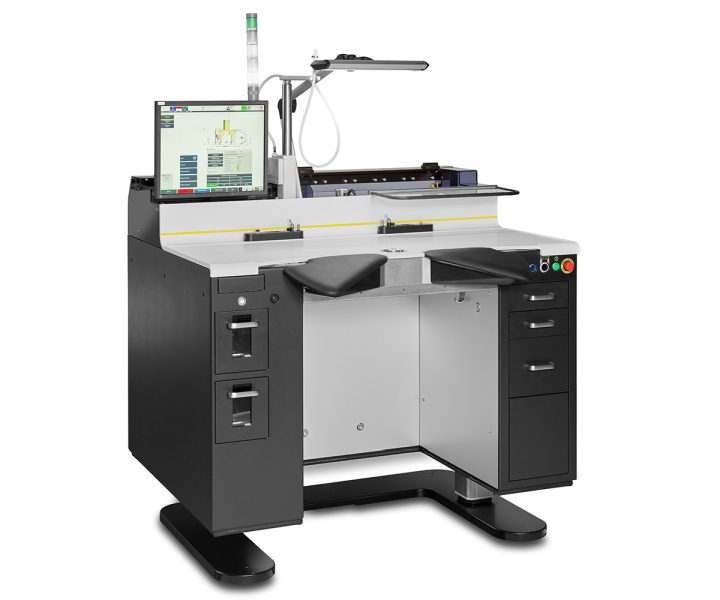
Montagestation für Uhrwerke. Im Innern verbirgt sich eine Montagefabrik im Miniaturformat (Bild: Precitrame).
Schlussendlich gelangen alle Uhrwerke in einen Lader im hinteren Bereich der Station, der sie vom Förderband hebt und für den folgenden Prozessschritt in eine weitere Einheit einlegt. Hier kann beispielsweise noch ein mikroskopisch feiner Tropfen Öl automatisch aufgebracht werden. Vor allem ist diese Einheit aber für die Qualitätssicherung zuständig. Es wird geprüft, ob die vorangegangenen Montageschritte mit der gewünschten Präzision gelungen sind. Alle Messdaten werden automatisch erfasst, über Canopen weitergeleitet und in einer Datenbank hinterlegt. Ein kleiner QR-Code auf dem Werkstückträger erlaubt die Zuordnung dieser Fertigungsdaten zur einzelnen Uhr. So entsteht für jedes einzelne Uhrwerk eine vollständige Dokumentation aller Montageschritte, die an dieser Station durchgeführt wurden.
Sanfte Beschleunigung
Der Vorgang »vom Förderband heben und einem Prozessschritt zuführen« stellt an die eingesetzte Technik beachtliche Anforderungen. Die filigranen Uhrwerke liegen lose in ihren flachen Trägern. Bei einer ruckartigen Bewegung könnten sie herausfallen, beschädigt werden und den Prozessablauf durcheinanderbringen. Zugleich sind im Vergleich zur Werkstückgröße beträchtliche Wege zurückzulegen. Der vertikale Hub des Laders etwa beträgt gut 20 Zentimeter. Seine Arbeit soll aber die Taktzeit der gesamten Maschine natürlich nicht verzögern. Also ist es nicht damit getan, die einzelnen Abläufe langsam und damit im sicheren Bereich durchzuführen.
Zudem sind drei Abläufe präzise zu synchronisieren: Die Transportpalette mit dem Werkstückträger wird auf einer horizontalen Achse zum Greifer befördert. Dieser fasst den Träger und wird vertikal nach oben geführt. Dort angekommen, fährt der Greifer wieder horizontal zur Messstation, wo die vorgesehene Routine abläuft. Für jede dieser Bewegungen wird ein genau abgestimmtes Profil benötigt: langsam anfahren, sanft beschleunigen, vorsichtig bremsen und den Vorgang in langsamem Tempo beenden. Die Antriebslösung für diese dreiachsige Bewegung hat Faulhaber speziell auf die Applikation abgestimmt.
Ihr Kernstück ist ein bürstenloser DC-Servomotor mit 4-Pol-Technologie der Serie 2250 BX4. Bei 22 Millimeter Durchmesser und circa 50 Millimeter Länge liefert er ein Drehmoment bis 32 Millinewtonmeter. Die integrierten Hall-Sensoren geben ein präzises Positionssignal an die Steuerung und bilden damit die Grundlage für exakt reproduzierbare Bewegungsabläufe. Da dieser Motor die Vertikalachse bewegt, verfügt er zudem über eine Bremse. Bei einer Prozessstörung, etwa einem Stromausfall, kann dadurch auch die Position gehalten und ein Herunterfallen des Greifers verhindert werden.
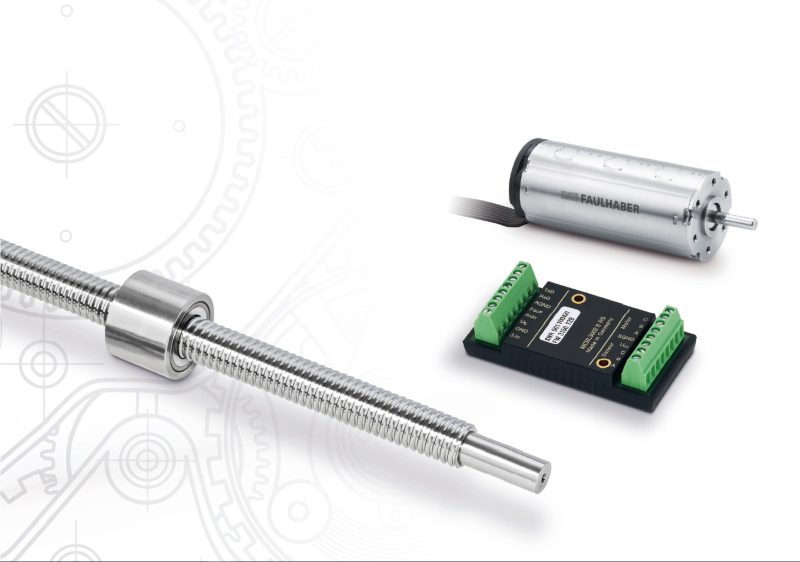
Treibende Kraft der Vertikalachse des Laders: kompakter DC-Servomotor mit Motion-Controller und Spindel mit besonders steilem Gewinde (Bild: Faulhaber).
Eine eigens für diese Anwendung entwickelte Spindel mit besonders steilem Gewinde der Faulhaber-Tochter MPS überträgt die Kraft des Motors auf die gesamte Strecke. Das Material für die Nuss, die auf der Spindel hin- und herfährt, wurde in aufwendigen Dauertests ermittelt: Der hochstabile Kunststoff PEEK hat sich dabei in drei Millionen Zyklen am besten bewährt.
Präzise Ansteuerung
Für das Abfahren der einzelnen Bewegungsabläufe ist der Profilgenerator zuständig – eine Software, die im Motion-Controller integriert ist. Die Parameter wurden von den Faulhaber-Experten direkt bei Precitrame auf die Applikation abgestimmt. Der Servomotor 2250 BX4 kann diese komplexe Aufgabe übernehmen und erfüllt auch die anderen Anforderungen, welche die Montagestation stellt. Er ist robust, langlebig und liefert ein hohes, rastfreies Drehmoment. Angesteuert wird er von einem MCBL 3002 SCO, einem kompakten Servo-Controller für bürstenlose DC-Motoren. Wegen der geringen Abmessungen von lediglich circa 47 Millimeter Länge, 23 Millimeter Breite und 7,5 Millimeter Tiefe wird ein solcher Controller in der Montagestation auch als zusätzlicher Canopen-Sensorknoten eingesetzt.
Für die beiden Horizontalachsen erwiesen sich die Motoren der Serie 2232 BX4 COD als geeignet. Hier ist die komplette Servoelektronik mit Canopen-Schnittstelle bereits im Motor integriert. Die Motoren liefern ein Drehmoment von 16 Millinewtonmetern. Ihr eisenloses Design eliminiert das Rastmoment. Das »Ruckeln« bei jeder Umdrehung, das bei Elektromotoren mit Eisenanker unvermeidlich ist, kann hier konstruktionsbedingt nicht entstehen. Das sorgt für einen sanften Transport der Uhrwerke.
Die gesamte Maschine entspricht den Dimensionen, in denen diese Branche arbeitet, und ist entsprechend kompakt bis filigran aufgebaut. Da je nach Ausführung bis zu drei Lader integriert werden müssen, wird der Platz noch knapper. Die Greifereinheit, die auf den drei Achsen bewegt wird, wiegt dennoch gut 600 Gramm. Von den Antrieben wird also eine hohe Leistung bei minimalem Volumen gefordert. Precitrame und sein Endkunde freuen sich über die gute Zusammenarbeit mit Faulhaber, dessen Antriebe und technische Unterstützung dazu beitrugen, dass die Montagestation ein Erfolgsmodell wurde.