Präzisionswerkzeuge entwickelt für hohe Drehzahlen
Es ist nicht leicht, etwas komplett unter Kontrolle zu bekommen – niemand weiß das besser als Figeac Aéro. Das Unternehmen mit Sitz im französischen Département Lot hat seine Maschinen zur Bearbeitung von Aluminiumlegierungen mit neuen Schneidwerkzeugen von Mitsubishi Materials bestückt, um die erwünschte Produktionssteigerung ohne Abstriche bei der Qualität zu erzielen.
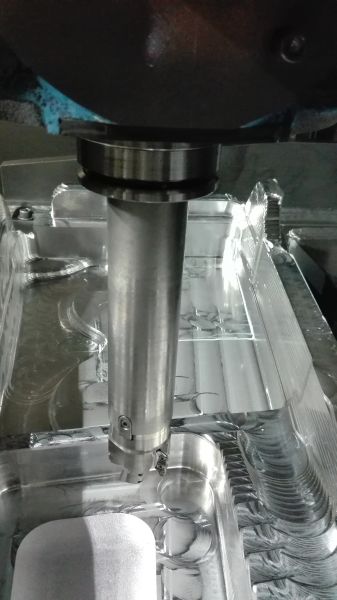
Hocheffiziente Aluminiumbearbeitung mit dem Fräser des Typs »AXD4000« von Mitsubishi Materials. Bild: Mitsubishi Materials
Mit gerade einmal 10.000 Einwohnern zählt Figeac im Allgemeinen nicht zu den bekannten Orten Frankreichs. Innerhalb der Branche jedoch ist das Städtchen als Heimat einiger der profiliertesten Luftfahrtunternehmen bekannt, allen voran Figeac Aéro. Der führende französische Zulieferer folgt in seiner Entwicklung Luftfahrtunternehmen wie Airbus und baut daher seine Produktivität aus. Die Wachstumsprognosen, die Nicolas Geneteaud, Marketing Communication and Business Investor Relations Manager, präsentiert, sprechen eine deutliche Sprache: »Betrug der Umsatz im Geschäftsjahr 2018 noch 371 Millionen Euro, peilen wir für 2019 mittlerweile 425 Millionen Euro an, für 2020 520 und für 2023 650 Millionen Euro.«
Die Zeichen stehen also auf unglaublich schnelles Wachstum. Seit seiner Gründung durch Jean-Claude Maillard im Jahr 1989 hat sich das Unternehmen in gerade einmal 30 Jahren zu einem führenden Luftfahrtzulieferer entwickelt und verfügt neben seinem Gründungsstandort in der Region Lot mittlerweile über 14 Produktionsstätten in aller Welt. »Als ich im Jahr 2000 zum Unternehmen kam, waren im Werk Figeac 120 Mitarbeiter beschäftigt, heute sind es etwa 1200«, erzählt Jean-Marie Morel, Cutting Tools Manager bei der Geschäftseinheit Strukturbauteile. Insgesamt beschäftigt das Unternehmen weltweit mittlerweile 3300 Mitarbeiter, 2000 davon in Frankreich.
Natürlich kann man Unternehmen mit technischer Kompetenz und ergänzendem Knowhow übernehmen und hochqualifizierte Mitarbeiter direkt ins Unternehmen holen, doch das allein ist nicht genug. Auch die Produktionsressourcen müssen laufend angepasst werden, um die »explodierende Produktionsnachfrage« zu bedienen, wie Baptiste Chevalier, Cutting Tools Manager bei der Geschäftseinheit Triebwerke, es formuliert. Allein in Figeac wurde in den letzten 20 Jahren etwa ein Dutzend Fertigungswerkstätten eingerichtet, um Teile und Baugruppen für wichtige Flugzeugtypen wie Airbus A350 (Böden und Triebwerkspylone) oder Boeing 787 (Türmechanismen, Verriegelungssysteme) herzustellen. »Wir liefern vor allem Teile für große Verkehrsflugzeuge mit mehr als 100 Sitzen«, erläutert Chevalier. Neben Baugruppen fertigt Figeac Aéro auch Strukturbauteile wie Rumpflängsholme, die eine Länge von über 10 Metern erreichen können, und die dazugehörigen Titanrippen, Rahmen, Bodenschienen, Triebwerksgehäuse, Fahrwerksteile sowie andere Teile. Die ohnehin schon lange Liste erweitert sich im Zuge von neuen Vertragsabschlüssen wie beispielsweise mit MHI Canada Aérospace im vergangenen November ständig. Auch für das »Global Express«-Businessjet-Programm von Bombardier wird das Unternehmen Teile und Baugruppen liefern.
Einschränkungen bei der Metallbearbeitung
»Dass eine immer höhere Produktion von Teilen aus Aluminium, Titan und anderen schwer zu bearbeitenden Werkstoffen aufgrund des erheblichen Materialabtrags und der unverändert hohen Qualitätsansprüche schwierig ist, ist kein Geheimnis. Dieses Wissen aber in der Praxis umzusetzen, ist alles andere als einfach, zumal unser bisheriger Schneidwerkzeuganbieter sich 2014 unsicher über die Weiterentwicklung der eigenen Produkte geäußert hat. Kurz gesagt, wir konnten uns nicht sicher sein, dass die zukünftigen Schneidwerkzeuge unseres Anbieters den Ansprüchen unserer Maschinen weiterhin entsprechen würden. Da wir uns dieses Risiko nicht leisten konnten, mussten wir einen anderen Anbieter finden«, erklärt Morel.
Für Figeac Aéro stand daher an erster Stelle sicherzustellen, angesichts des gestiegenen Produktionsbedarfs auch weiterhin moderne und zuverlässige Schneidwerkzeuge einsetzen zu können. Dies galt vor allem, weil zuvor zwei neue Werkzeugmaschinen mit einer Spindelleistung von 120 Kilowatt aufgestellt wurden. Die alten Schneidwerkzeuge waren bis 22.000 Umdrehungen pro Minute einsetzbar. Baptiste Chevalier war damit nicht zufrieden: »Für die neuen Maschinen benötigten wir Werkzeuge, die auch bis 33.000 Umdrehungen pro Minute funktionieren. Außerdem haben wir uns überlegt, wie wir die Werkzeuge am Standort Figeac standardisieren können, um die Bestände zu verschlanken, die Werkzeugverfügbarkeit zu steigern und die Kosten zu senken.«
So kam der Konzern zu Mitsubishi Materials. »Die Werkzeuge mussten unbedingt in den 120-Kilowatt-Spindeln eingesetzt werden können und zu unseren bestehenden Werkzeughaltern passen. Außerdem musste der Anbieter unsere Produktionssteigerung mitgehen können. Mitsubishi Materials ist ein internationaler Anbieter und hatte genau die richtige Lösung für uns.«
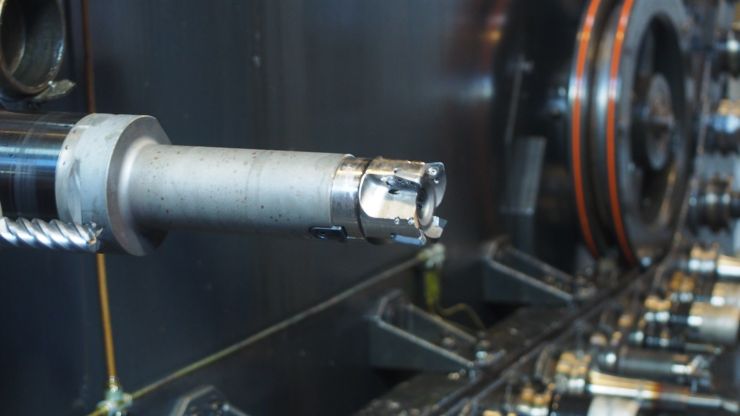
Das neue Schneidwerkzeug wurde besonders für die Aluminiumbearbeitung bei hohen Drehzahlen und Vorschüben konzipiert. Bild: Mitsubishi Materials
Ein Werkzeug, das den Anforderungen gewachsen ist
Metallbearbeitung ist die Kernkompetenz von Figeac Aéro. Das Personal in den Abteilungen des Konzerns arbeitet an verschiedenen Fertigungsanlagen und weiß genau, worauf es ankommt. In enger Abstimmung mit Laurent Le Méteil, Aeronautics Business Manager, und Grégory Lafon, Application Technician, (beide bei MMC Metal France) konnte das Team das Schneidwerkzeug des Typs »AXD4000« testen, das speziell für die Aluminiumbearbeitung bei hohen Drehzahlen und Vorschüben konzipiert ist. »Dieses Schneidwerkzeug ist eine Spezialentwicklung aus Japan und entstand in Zusammenarbeit mit Makino, dem Hersteller der zwei besonders leistungsfähigen neuen Maschinen in unserer Werkstatt. Es kann bei Spindeldrehzahlen bis 35.000 Umdrehungen pro Minute uneingeschränkt verwendet werden. Dank dieser Zusammenarbeit in der Entwicklung und Konzeption konnten wir die bestmögliche Balance zwischen schierer Leistung einerseits und höherer Stabilität und Sicherheit andererseits finden«, so Lafon. »Die Wendeschneidplatten werden mit zwei Schrauben sicher im Werkzeugkörper fixiert. Hierdurch wird nicht nur ein Herausschleudern der Schneidplatte verhindert, sondern auch eine präzise Positionierung ermöglicht. Dadurch verlängert sich zum einen die Standzeit des Werkzeugs, zum anderen wird eine herausragende Oberflächengüte an den Teilen sichergestellt.
Doch die Werkzeuge bieten noch weitere Vorteile. So sind die Winkel beim Tauchfräsen aggressiv genug eingestellt, um in erheblichem Umfang Bearbeitungszeit pro Komponente zu sparen, und das ohne Abstriche bei der Werkzeugstandzeit. Bei der Werkzeuggeometrie wurde auf eine Auslegung der Spankammer geachtet, die effiziente Spanabfuhr ohne Beeinträchtigung der Festigkeit des Werkzeugkörpers sicherstellt. Vor allem sind die Werkzeugkörper in Durchmessern von 20 bis 125 Millimeter erhältlich und die angebotenen Wendeschneidplatten sind mit verschiedenen Eckradien von 0,4 bis 5 Millimeter erhältlich. »Dank seiner langen Standzeit macht es uns dieses Werkzeug möglich, weitestgehend standardisierte Wendeschneidplatten einzusetzen«, bekräftigt Morel. »Wir konnten die Bestände und die Anzahl der verschiedenen Wendeschneidplatten verringern. Jetzt kommen wir mit nur zwei Geometrien für ein einzelnes Werkzeug aus. Diese lassen sich zudem an den neuen Spindeln ebenso wie an den alten Maschinen einsetzen.« Baptiste Chevalier ergänzt: »Wir müssen nur das Schneidwerkzeug austauschen. Die ursprünglichen Zerspanvolumina konnten dank des Entwicklungsteams von Mitsubishi Materials beibehalten werden. Insgesamt konnten wir dank der Leistung des AXD4000-Schneidwerkzeugs mit der enormen Produktionssteigerung mithalten. Die Wendeschneidplatten erreichen jetzt etwa 25 Prozent längere Standzeiten und es kommt viel seltener zu Brüchen.«
Laurent Le Méteil ergänzt, dass Mitsubishi Materials im Rahmen der zweiten Projektphase die Aufsteckhalter für das gesamte Sortiment an Produkten für die Metallbearbeitung anpassen konnte. »Es gab grünes Licht aus Japan, das Schneidwerkzeug auch in anderen Größen bereitzustellen. Wir haben spezielle Pläne ausgearbeitet und die Durchmessertoleranzen so angepasst, dass unsere Werkzeuge für alle Teile bei Figeac Aéro einsetzbar sind.«