Prozessoptimierung durch Echtzeit-Daten
Werkzeugverwaltung, -voreinstellung
Digitale Vernetzung ist das Trendthema der Industrie. Viele Praktiker in mittelständischen Unternehmen setzen das Schlagwort »Industrie 4.0« mit einem hohen Grad an Komplexität gleich und sind verunsichert. Häufig ist unklar, was sie darunter konkret für den eigenen betrieblichen Alltag und für ihre zukunftssichere Produktionsstrategie und Produktionsplanung erwarten können.
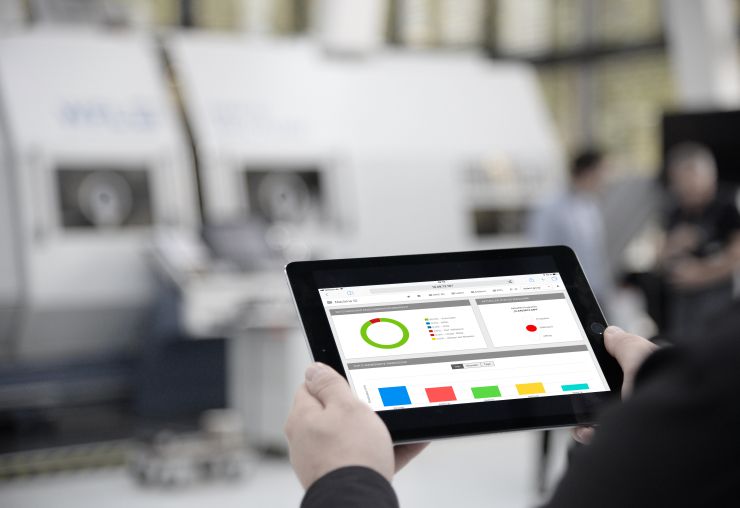
Alle relevanten Daten werden übersichtlich angeordnet und lassen sich nach unterschiedlichen Kriterien analysieren oder darstellen. Bild: Walter
Der Zerspanungsspezialist Walter hat sich bereits vor einigen Jahren dazu entschlossen, den Themenkomplex Digitalisierung anzugehen, und bietet unter der Produktlinie »Walter Nexxt« digitale Produkte und Industrie-4.0-Lösungen für den Einsatz in mittelständischen Unternehmen an. Statt auf eine komplett automatisierte Fabrik setzt der Werkzeughersteller auf schrittweise Lösungen, um Zerspanungsprozesse zu optimieren, wie zum Beispiel mit der Schnittdatenoptimierungs-Software »Comara iCut« und der Fertigungsmonitoring-Plattform »Comara appCom«.
Schnittdaten-Optimierung nach Live-Daten
Automatisierung, Digitalisierung und vernetzte Prozesse gehören in vielen Bereichen der industriellen Produktion schon lange zum Alltag. Durch die Leistungssprünge, die Hard- und Software für die Erhebung und Analyse von Live-Daten gemacht haben, ergeben sich neue Möglichkeiten, Prozesse weiter zu optimieren. Auf der Echtzeitanalyse eingehender Maschinendaten basiert zum Beispiel das Software-Tool Icut. Walters Softwarepartner Comara hat mit dieser adaptiven Vorschubregelung nicht das Fräsen oder Drehen neu erfunden, sondern sich damit auf eine sehr konkrete Problemstellung fokussiert: Wie kann man, ohne massive Eingriffe in den bestehenden Prozess oder aufwendige Programmierung, das Optimum aus einer Maschine herausholen? Das Ergebnis ist eine Software, mit der sich die Bearbeitungszeit für das Fräsen pro Werkstück weiter reduzieren lässt.
Die Software wird einfach in das vorhandene Steuerungsprogramm integriert und übernimmt die Daten für den Bearbeitungsprozess. Im ersten Schnitt »lernt« das Programm die Leerlaufleistung der Spindel und die maximale Zerspanleistung pro Schnitt. Ab dann misst sie die Spindelleistung bis zu 500 Mal pro Sekunde und passt den Vorschub automatisch an. So fährt die Maschine, wenn immer möglich, den maximalen Vorschub, den die Software je Werkzeug »gelernt« hat. Ändern sich die Schnittbedingungen, zum Beispiel durch unterschiedliche Fräserumschlingungen und Spantiefen, Aufmaßschwankungen oder durch Verschleißerscheinungen am Werkzeug, passt sie Geschwindigkeit und Leistung in Echtzeit an – mit positivem Effekt, und das nicht nur für die Bearbeitungszeit eines Werkstückes.
Durch das optimierte Fräsverhalten erhöht sich auch die Prozesssicherheit. Auf die Spindel wirken die Kräfte konstanter, was ihre Lebensdauer erhöht. Droht das Werkzeug aufgrund zu hoher Spindellast zu brechen, reduziert das Programm sofort den Vorschub oder stoppt die Aktion ganz. So konnten bei Kunden schon erstaunliche Effizienzsteigerungen erreicht werden. Passt die Bearbeitung, sind um die zehn Prozent Reduktion bei der Bearbeitungszeit im Regelfall möglich, es wurde aber auch schon das Doppelte geschafft. Bei hoher Stückzahl wird so einiges an Maschinenkapazität frei. Die Software arbeitet auch ohne den Einsatz von Walter-Werkzeugen, nur die Systemvoraussetzungen der Maschine müssen gegeben sein.
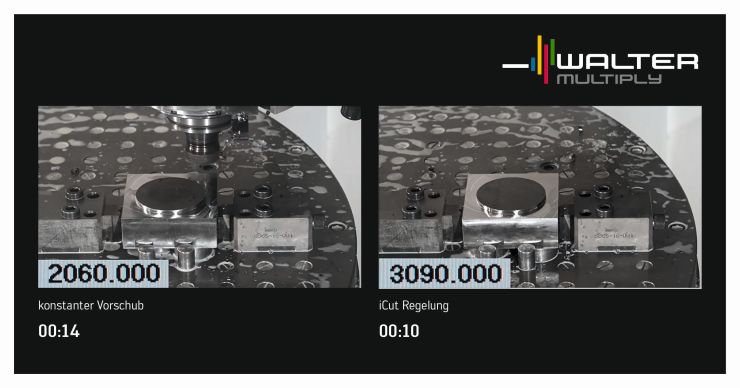
»Comara iCut« passt den Vorschub dynamisch den Schnittbedingungen an. Pro Werkstück lässt sich sowohl die Fertigungszeit reduzieren als auch die Prozesssicherheit erhöhen. Bild: Walter
Mehr Prozesssicherheit und Effizienz
Haben sich die Softwarespezialisten bei Icut auf die Optimierung eines ganz bestimmten, eng definierten Prozesses konzentriert, wurde die Appcom-Softwareplattform entwickelt, um die komplette Datenmenge, die eine Maschine während der Bearbeitungsprozesse erzeugt, für die Prozessoptimierung nutzbar zu machen – und das so einfach und übersichtlich wie möglich. Die Lösung besteht dabei aus zwei Komponenten: einem PC, der in die Maschinen eingebaut und in die Steuerung integriert wird, sowie der Software, die Daten analysiert und visualisiert. Der Werkzeughersteller aus Tübingen nutzt dafür das App-Prinzip: In der Grundausstattung verfügt Appcom bereits über 13 Anwendungen, mit denen sich die wichtigsten Parameter für eine Optimierung der Prozesse erheben und überwachen lassen. Dazu gehören der Status der beobachteten Maschinen, ihre Produktivität, Zuständigkeiten sowie die Laufzeitstabilität der gefahrenen Programme. Alle wichtigen Kennzahlen, Berichte und Monitoring-Daten werden optisch übersichtlich und einfach verständlich aufbereitet.
Zugriffsrechte individuell zuweisen
Wer diese Daten zu Gesicht bekommen soll, lässt sich individuell zuweisen. So sieht der Maschinenführer nur die Daten und Berichte, die für ihn relevant sind. Produktions- und planungsverantwortliche Manager können dagegen alle Monitoring-Möglichkeiten nutzen. Angezeigt werden die Apps in einem Web-basierten Interface, auf das via stationärer PCs, aber auch mit allen gängigen mobilen Endgeräten zugegriffen werden kann. Es lassen sich sowohl aktuelle Probleme und kritische Prozesse identifizieren, die auf einer Maschine laufen, als auch der gesamte Zerspanungsprozess analysieren. Parameter sind beispielsweise Effizienz, Kosten pro Werkzeug oder pro Werkstück sowie Prozesssicherheit. Für die Optimierung und Planung der Produktion lassen sich so Live-Daten nutzen, die nicht manuell aus unterschiedlichen Monitoring-Programmen, Datenformaten und Datenquellen zusammengeführt werden müssen. Die Lösung lässt sich außerdem mit ERP-Systemen verbinden, beispielsweise, um Daten dorthin zurückzuspielen oder Datensätze einzulesen. Die so eingespielten Daten können dann von einer App aufbereitet und mit den Maschinendaten verbunden werden. Ein weiterer Vorteil: Appcom arbeitet ohne Anbindung an eine Cloud. Unternehmenskritische Daten liegen auf dem PC und, wenn gewünscht, auf den unternehmenseigenen Servern, und nicht in einer Cloud, weder von Walter, noch von Comara, noch von einem anderen Anbieter.
Für Zerspanungsbetriebe, die meist unter Kosten- und Effizienzdruck stehen, ist das Potenzial hoch, das sich durch den Einsatz von Monitoring- und Analyse-Tools wie Appcom ergibt. Konkrete Zahlen lassen sich dazu aber nur schwierig angeben. Das Effizienz- und Einsparungspotenzial aus dem Einsatz einer Monitoring- und Analyseplattform hängt von unterschiedlichen Faktoren ab. Wichtig ist der Automatisierungs- und Digitalisierungsgrad der Produktionsprozesse, aber auch, wie problemkritisch die Bearbeitung selbst ist. Die bisherige Erfahrung bei Walter ist, dass Kunden, die die Lösung nutzen, Produktivität und Prozesssicherheit pro Maschine deutlich wahrnehmbar steigern.