Drehwerkzeuge – jede Sekunde zählt
Drehwerkzeuge, galvan. Diamantwerkzeuge PKD-CBN
Sechsstellige Stückzahlen, kurze Taktzeiten und Sonderwerkzeuge. Die Serienfertigung von hohen Losgrößen stellt kleine Lohnfertiger vor große Herausforderungen. Der Belgier Chris Martin stellt sich mit seinem Unternehmen Amalo täglich diesen Aufgaben. »Für uns zählt jede Sekunde, die wir einsparen können«, so Martin. Hierfür setzt er auf Werkzeuglösungen der Paul Horn GmbH. Neben Standardwerkzeugen kommen auf seinen Maschinen auch zahlreiche Sonderlösungen zum Einsatz.
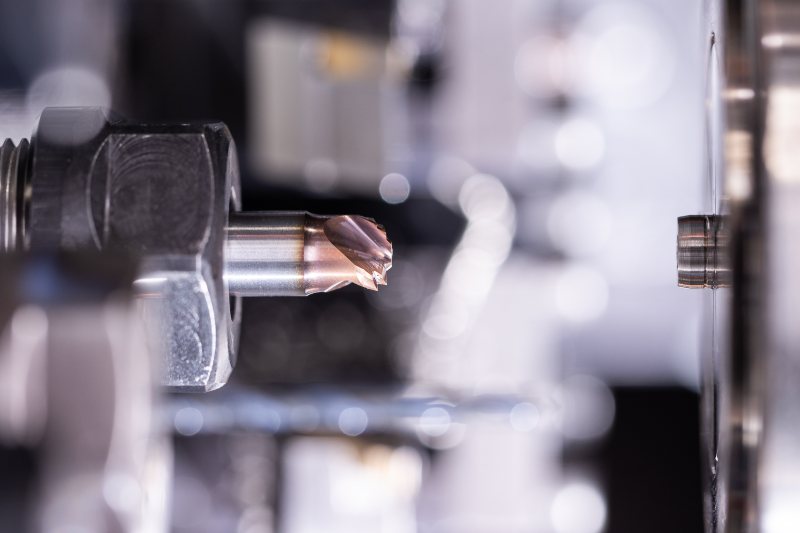
Toleranzen im Mikrometerbereich lassen sich durch den profilierten Vollhartmetallfräser in unbeaufsichtigter Fertigung prozesssicher einhalten. Das VHM-Frässystem lässt sich an zahlreiche Sonderaufgaben anpassen (Bild: Horn/Sauerman).
Der Startschuss fiel im Jahr 2010. Mit seinem Unternehmen Amalo ist Chris Martin ein universeller Teilefertiger aus dem belgischen Ingelmunster in der Nähe von Brügge. Er hat sich auf Drehteile bis zu einem Durchmesser von 65 Millimetern spezialisiert. Hier reiht er sich jedoch nicht zwischen all den anderen Lohnfertigern ein, denn der Betrieb produziert Bauteile, bei denen sich andere die Zähne ausbeißen: Teile mit hohen geometrischen Anforderungen, sehr engen Toleranzen und Oberflächengüten bis zum Spiegelglanz. Hierzu zählen etwa Präzisionsdrehteile für den Fadendurchlass an Webmaschinen sowie weitere technische Hochpräzisionsteile für Textilmaschinen. Ebenso produziert das Unternehmen Bauteile für komplexe Waschdüsen für die Reinigungs- und chemische Industrie, Designteile als Spiegelglanzteile für Verpackungen sowie Kunststoffteile für besondere chemische und mechanische Belastungen.
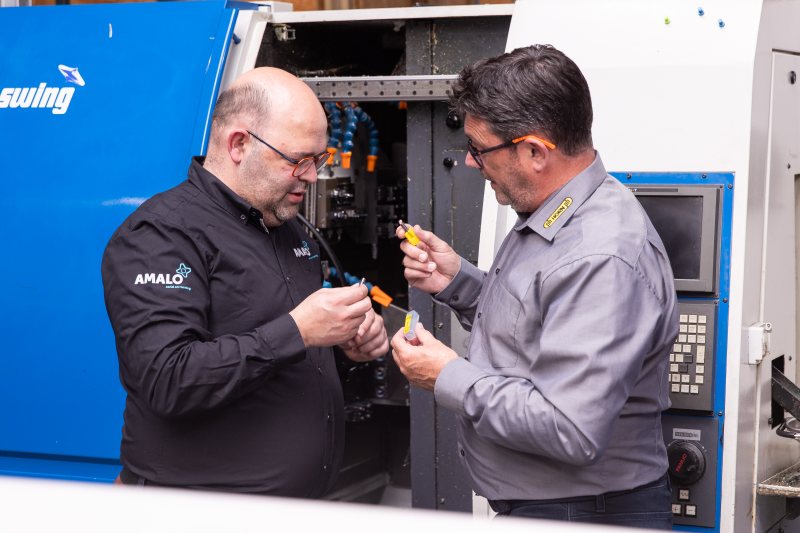
Ständig auf der Suche nach der besten Werkzeuglösung: Chris Martin (li.) in der Diskussion mit dem Horn-Techniker Kees van Bers (Bild: Horn/Sauerman).
Co-Engineering
Bevor bei Amalo ein Teil in Serie geht, steht die sorgfältige Analyse des zu produzierenden Bauteils an. »Wir schauen genau hin, wo wir bei welcher Bearbeitung wertvolle Zeit einsparen können. Hierzu prüfen wir von Anfang an die Möglichkeit, Sonderwerkzeuge einzusetzen«, erzählt Martin. Dabei bietet er seinen Kunden auch das Co-Engineering an. Dazu zählen beispielsweise Optimierungsmöglichkeiten, welche die Stückkosten weiter senken könnten. Auch der Einsatz von alternativen Werkstoffen mit der gleichen Funktionalität oder ein anderer Ansatz mit weniger Abfall spielt hier eine Rolle. Der Fertiger profitiert dabei von der langjährigen Erfahrung in der Serienfertigung von komplexen und hochpräzisen Bauteilen.
Fräs- statt Drehwerkzeug
Eine genaue Analyse fand auch bei einem Bauteil für den Maschinenbau statt. Amalo fertigt von diesem Teil in Serie rund 300.000 Stück pro Jahr. »Aufgrund der hohen Stückzahl achteten wir bei der Auslegung des Fertigungsprozesses auf jede Sekunde sowie auf die Maßhaltigkeit der eingesetzten Werkzeuge«, erläutert Martin.
Gerade die Maßhaltigkeit spielt eine große Rolle, da die Maschine auch ohne Personal über Nacht produziert. Ein Knackpunkt zur Fertigung des Bauteils ist der Axialeinstich. Die Tiefe des Einstichs ist mit +0,015 Millimetern und der Durchmesser mit +0,020 Millimetern toleriert – Toleranzen, die in der mannlosen Fertigung in Serie kaum einzuhalten sind. »Für die kritischen Maße suchten wir von Anfang an die passende Werkzeuglösung«, sagt Martin.
Die Lösung lieferte Horn nicht mit einem Drehwerkzeug, sondern mit einem profilierten Fräswerkzeug des Werkzeugsystems »DS«. Der dreischneidige Fräser fungiert im Einsatz wie eine Art Flachsenker und fertigt den Axialeinstich mit Fasen in einem Eintauchvorgang. »Durch den Einsatz haben wir neben dem Zeitvorteil auch den Vorteil der Maßhaltigkeit und der Standzeit. Bei der Fertigung ist jeder Einstich gleich und perfekt in der Toleranz«, erzählt Martin.
Ideal für Edelstahl
Für die Fertigung von Nuten an einem anderen Bauteil setzt Martin auf das dreischneidige »System 315«. Die Nuten dienen im späteren Einsatz als Klebenuten. Für die Serienfertigung legten die Horn-Techniker das Sonderwerkzeug mit einem präzisionsgeschliffenen Profil aus. Das Werkzeug fertigt die vier Nuten parallel mit einem Einstich. Für den Einsatz in Edelstahl kommt hierbei die Beschichtung »IG35« zum Einsatz. Mit dieser Werkzeugbeschichtung bieten Werkzeugsysteme des Tübinger Herstellers eine hohe Leistung und lange Standzeiten bei der Bearbeitung von rostfreien Stählen, Titan- und Superlegierungen.
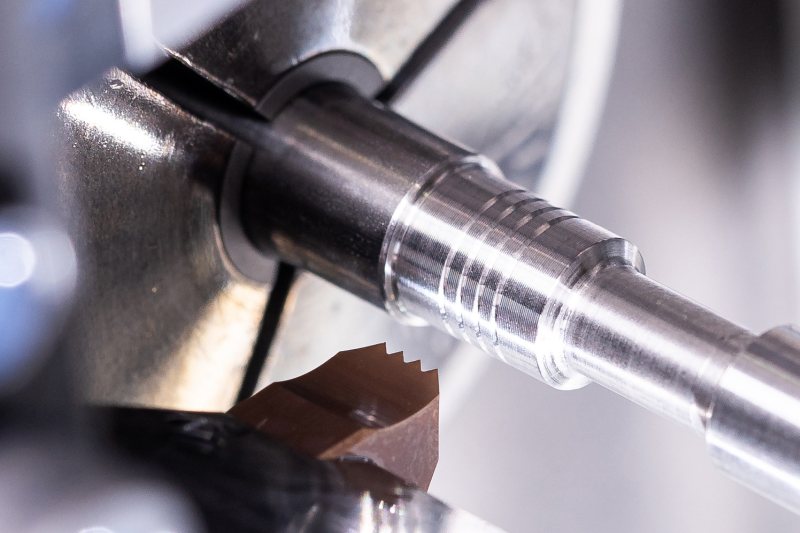
Wenn jede Sekunde zählt, lassen sich mit dem »System 315« auch vier Einstiche gleichzeitig fertigen (Bild: Horn/Sauerman).
Die Aluminium-Titansiliziumnitrid-Schicht hemmt die Bildung von Aufbauschneiden durch die geringen Reibwerte. Aufgrund der HiPIMS-Beschichtungstechnologie weist die Schicht sehr glatte Eigenschaften und eine hohe Warmfestigkeit auf. Des Weiteren ist die Werkzeugschicht frei von Schichtdefekten wie Droplets oder anderen Schichtfehlern an der Schneidkante.
Volle Prozesssicherheit
Eine weitere Aufgabe, die nicht einfach zu lösen war, stellte Chris Martin und den Horn-Techniker Kees van Bers vor ein Problem, welches noch mehr Aufwand, Ideen und ein weiteres besonderes Werkzeug erforderte. Hierbei handelt es sich um das Innenausdrehen einer speziellen Düse aus Reinaluminium. Die Innenkontur verläuft konisch auf einer Länge von 24 Millimetern, von Durchmesser acht bis Durchmesser drei Millimeter zu. Gefordert ist eine Toleranz von acht Mikrometern mit einer Rautiefe von nur Ra 0,8.
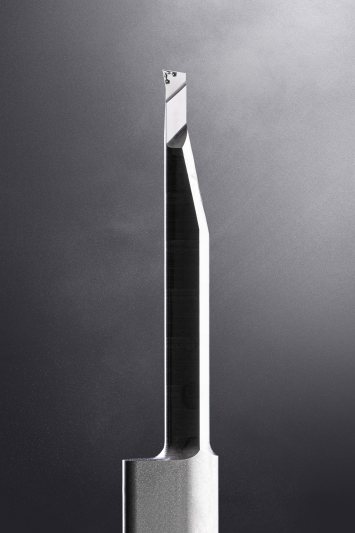
Mit einer gelaserten Spanleitstufe konnte Horn die Spanprobleme lösen (Bild: Horn/Sauerman).
»Das Standardwerkzeug führte im Einsatz zu langen Wirrspänen und einem Späneknäuel. Diese verkratzten die Oberfläche und führten sogar teilweise zum Werkzeugbruch«, erinnert sich van Bers. Auch die Programmierung von kurzen Entspanungszyklen führte zu keiner entscheidenden Verbesserung. Die Prozesssicherheit gelang dem Werkzeughersteller mit dem Einsatz eines Werkzeugs aus der Reihe »Supermini Typ 110« mit einer gelaserten Spanleitstufe. Die Ergebnisse waren ein prozesssicherer Spanbruch, Späne in Millimetergröße, die geforderte Oberflächenqualität und die Maßeinhaltung der Toleranzen sowie die erhoffte Prozesssicherheit.
Volle Spankontrolle
Im Juni 2024 stellte der Werkzeugspezialist eine gesinterte Spanformgeometrie für den »Supermini Typ 105« vor. Eine der größten Herausforderungen bei der Innenbearbeitung sind lange Späne. Die Bohrungsbearbeitung führt, je nach Werkstoff, oftmals zu langen Spänen. Sie wickeln sich um das Werkzeug, verstopfen Bohrungen oder führen im schlechtesten Fall zum Werkzeugbruch. Hier kann die Spanformgeometrie Abhilfe schaffen. Sie leitet und formt den Span und bringt ihn zum Bruch.
Bisher kamen hierzu speziell gelaserte oder geschliffene Spanformgeometrien zum Einsatz. Dies war jedoch mit einem entsprechenden Kostenfaktor der Schneidplatte verbunden. Mit dem neuen »Supermini Typ 105« hat es der Werkzeughersteller geschafft, ein universelles Ausdrehwerkzeug mit gesinterter Spanformgeometrie zu entwickeln. Das Werkzeug bietet im Einsatz eine hohe Prozesssicherheit durch die gute Spankontrolle. Die Schneidengeometrie reicht weit in den Eckenradius der Schneidplatte. Dies stellt die Spankontrolle auch bei kleinen Zustellungen sicher. Die Geometrie lässt sich universell für verschiedene Werkstoffgruppen einsetzen und eignet sich zum Innen-, Plan-, Kopier- und Rückwärtsdrehen.
Die enge Zusammenarbeit zwischen beiden Unternehmen besteht seit dem Jahr 2010. Zahlreiche Zerspanaufgaben von Chris Martin konnte der Tübinger Werkzeughersteller in dieser Zeit lösen. »Ich schätze die Zusammenarbeit mit den Technikern von Horn sehr. Genau wie ich, versucht Horn ständig, das Maximale aus der jeweiligen Aufgabe herauszuholen«, resümiert Martin.