Fertigen mit Ultraschall
Bearbeitungszentren
Ein neues Bearbeitungszentrum ist leistungsfähig und präzise, aber nicht käuflich. Geht es um additive Fertigung, ist Hermle nämlich Dienstleister.
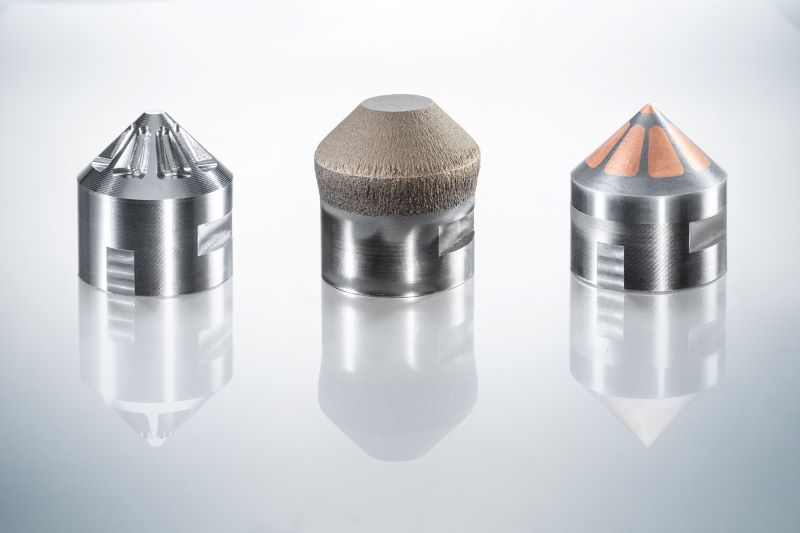
Der Vorteil hybrider Fertigung: Nach dem Ausfräsen der Taschen wird Kupferpulver aufgetragen. Im Anschluss wird überflüssiges Material spanend abgetragen (Bild: Hermle).
Beim neuen Bearbeitungszentrum »MPA 42« von Hermle verlassen die Rohlinge den Arbeitsraum der Zerspanungsmaschine mit mehr Masse statt mit weniger. Denn das Kürzel »MPA« steht für das »Metall-Pulver-Auftrag-Verfahren«, das der Maschinenhersteller vor rund sieben Jahren zur Marktreife gebracht hat. Das neue Bearbeitungszentrum steht bei der Hermle Maschinenbau GmbH in Ottobrunn, einer hundertprozentigen Tochterfirma der Maschinenfabrik Berthold Hermle AG. Das Tochterunternehmen hat sich mittlerweile zu einem Dienstleister für die additive Fertigung entwickelt.
Geschäftsführer Rudolf Derntl öffnet die Türen der Schallschutzumhausung der neuen Maschine, hinter der sich ein stark modifiziertes 5-Achs-Bearbeitungszentrum vom Typ »C 42 U« verbirgt. Neben der Spindel ragt eine Lavaldüse in den Arbeitsraum, eine Sprüheinheit für Kühlschmiermittel fehlt dagegen. »Die Düse beschleunigt das Pulver und schießt es gezielt auf den aufgespannten Metallrohling«, erklärt Derntl. Überhitzter Wasserdampf und Stickstoff spielen eine ebenso wichtige Rolle wie die Düsengeometrie, damit das Pulver Überschallgeschwindigkeit erreicht und sich durch die Deformation beim Aufprall verbindet. Ein Dampferzeuger und fünf Pulverförderer finden im hinteren Teil der Maschine Platz. Allen Auftragsmaterialien und Rohlingen gleich ist ihre Duktilität: »Es funktionieren sehr viele Metalle, da der Auftrag auf plastischer Verformung basiert. Demnach muss auch die Oberfläche der Halbzeuge duktil sein«, ergänzt der Geschäftsführer. Zum Einsatz kommen in der Regel neben im Werkzeugbau üblichen Warm- und Kaltarbeitsstählen mit hohem Kohlenstoffanteil auch Kupfer und Ampcoloy.
Materialmix für den Spritzguss
Kupfer leitet die Wärme deutlich schneller ab als die verarbeiteten Werkzeugstähle. Für die Konstruktion von Spritzgussformen hat daher die Materialkombination aus Stahl und Kupfer einen entscheidenden Vorteil: »Mit der additiven Fertigung bringen wir Kupfer an die Stellen des Werkzeugs ein, die für Kühlkanäle keinen Platz haben. Der Kupferkern leitet beim Spritzgießen die Wärme an den nächstgelegenen Kühlkanal schneller ab als Stahl. Anwender sparen dadurch wertvolle Sekunden bei der Kühlzeit, und die Oberflächenqualität der Kunststoffteile verbessert sich«, führt Derntl aus.
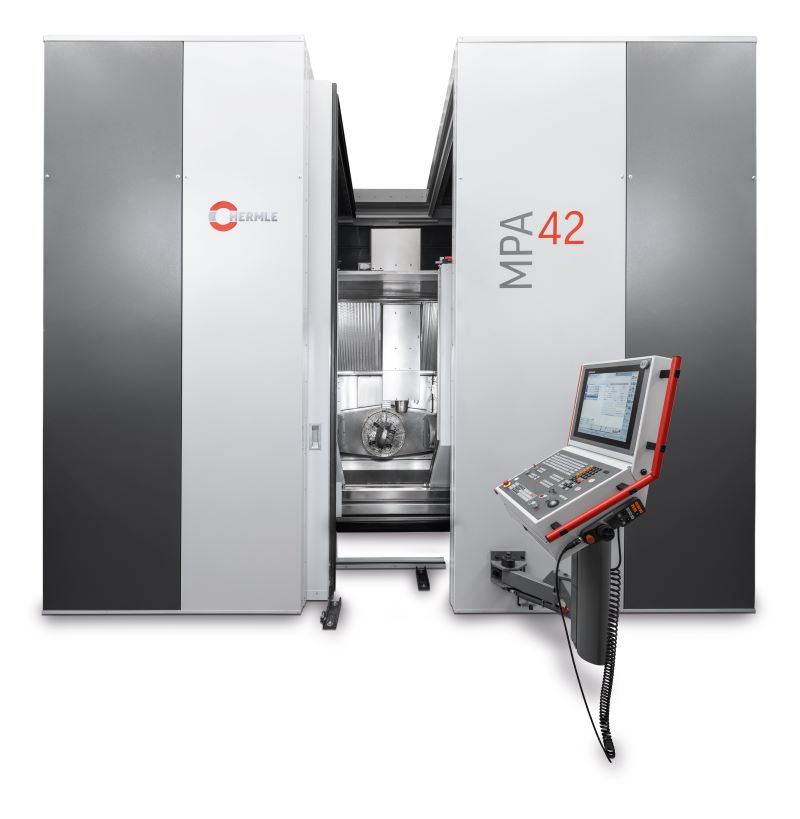
Das neue Bearbeitungszentrum verbindet den additiven Materialaufbau mit hochpräziser Zerspanung (Bild: Hermle).
Die fünf Achsen des Bearbeitungszentrums erlauben eine nahezu beliebige Ausrichtung des Pulverstrahls zum Bauteil und sorgen dabei für eine maximale Gestaltungsfreiheit. Kühlkanäle können damit direkt auf den gekrümmten Oberflächen eines Rohlings aufgebaut werden. So erhalten auch größere Spritzgussformen eine konturnahe Kühlung, ohne das gesamte Bauteil additiv aufzubauen. Grenzen setzt lediglich der Arbeitsraum. »Je nach Geometrie liegt das Größenlimit für den additiven Prozess bei je 600 Millimetern in Länge und Breite. In der Regel sind die Bauteile jedoch kleiner«, erläutert Derntl. Besonders eignet sich die Maschine auch zur Herstellung zylindrischer oder konischer Bauteile wie gekühlten Vorkammerbuchsen. Durch Materialauftrag bei rotierendem Bauteil werden Taschen und Kanäle effizient gefüllt und mit Werkzeugstahl eingeschlossen. Neben der Realisierung effizienter Kühlungen bietet das »MPA«-Verfahren noch weitere interessante Anwendungsmöglichkeiten. Viele Materialien verdichten sich durch den Auftrag derart, dass sich die Bauteiloberflächen auf Hochglanz polieren lassen. Mit dem Verfahren können auch Funktionselemente wie Heizdrähte oder Sensoren zur Temperaturüberwachung der Kavität in Stahl oder Kupfer eingebettet und damit in das Werkzeug integriert werden, zum Beispiel für eine variotherme Temperaturführung. Das Wissen, wo Materialkombinationen Sinn ergeben, wie Kühlkanäle und Funktionselemente am besten angelegt werden und die Möglichkeit, Formwerkzeuge einteilig zu bauen, ist die Stärke der Hermle Maschinenbau GmbH. »Wir verkaufen keine Maschinen, sondern Knowhow«, erklärt der Geschäftsführer. Das Team aus Ottobrunn berät Konstrukteure von Spritzgusswerkzeugen, greift 3D-Modelle auf und optimiert durch Kühlkanal, Funktionselement oder Multimaterialkombination die später mit diesem Werkzeug gefertigten Spritzgussteile. »Es geht um reduzierte Taktzeiten und höhere Bauteilqualitäten, die mit anderen Technologien sonst nur schwer zu erreichen sind«, betont Derntl.
Software für Auf- und Abtrag
Mit einer eigenen CAM-Software generieren die Anwendungstechniker den Code für die Maschinensteuerung. Dies beinhaltet nicht nur die Bahnbewegungen, sondern auch die Pulvermengen, bestimmte Temperaturen und den Wechsel zwischen Materialaufbau und Fräsen. Dies wurde notwendig, da kein CAD/CAM-Hersteller den speziellen Prozess – Fräsen, Auftragen, Fräsen – abbilden konnte. Ist die Vorarbeit abgeschlossen, schickt der Anwender den Rohling nach Ottobrunn. So kommt das Bauteil schon mit gefrästen Kühlkanälen oder Taschen für den Kupferauftrag an. Der Rohling wird anschließend auf Maßhaltigkeit und ob die Konstruktionsvorgaben eingehalten wurden geprüft.

Nachdem die Kühlkanäle mit einem wasserlöslichen Metallpulver gefüllt sind, erfolgt der nächste Metallpulverauftrag (Bild: Hermle).
Vor Prozessbeginn kommt das Bauteil in die Heizstation und wird auf circa 300 Grad Celsius gebracht, denn sowohl Substrat als auch Metallpulver müssen für eine bessere Duktilität erhitzt werden. Die Energie zur Beschleunigung des Pulvers kommt aus dem Wasserdampf. Beim Durchgang beider Komponenten durch die Düse erreicht das Pulver die notwendige Überschallgeschwindigkeit. Damit auch während der Bearbeitung die Temperatur konstant bleibt, wird das Bauteil bis zum letzten Spanabtrag beheizt, um Temperaturgradienten zu verhindern, welche Spannungen, Risse oder Verzug bedeuten würden.
Auftragen, Zerspanen, Auftragen
Im Fertigungsprozess wird abwechselnd Material aufgetragen und zerspant. Nach dem Pulverauftrag werden Details wie feine Rippen in das neue Material gefräst, Kühlkanäle werden mit einem wasserlöslichen, metallenen Material gefüllt und per »MPA«-Auftrag wieder mit einer Stahlschicht verschlossen. Das Füllmaterial kann später im Wasserbad ausgespült werden, wodurch die gewünschten Hohlräume entstehen. Mit dem Pulverstrahl werden Aufbauraten von 200 bis 400 Kubikzentimeter pro Stunde erreicht, bei Kupfer sind nahezu 1000 Kubikzentimeter möglich. »Die neue Maschine ist das Herz unseres Dienstleistungsangebots«, betont Geschäftsführer Derntl. Ihm ist es wichtig, alle Prozesse im Haus abzubilden – von der Beratung, Optimierung und Machbarkeitsprüfung über die Werkstoffuntersuchung bis hin zum finalen Qualitätscheck. »Damit sind wir agil und schützen unser Knowhow sowie das unserer Kunden.«